We need metals every day. Scientists are discovering new technologies and methods every year to improve human commodities. Sheet metal fabrication is one of the most common terms in metal manufacturing.
However, compared to the nineteenth century, we have gone too far in today’s world. Industries are following a good number of metal fabrication techniques to improve productivity and cost. This article will bring you the sheet metal fabrication guide.
What is sheet metal fabrication?
Sheet metal fabrication involves slicing, punching, bending, and assembling flat steel or aluminium sheets into metal structures or items. Cutting and burning sheet metal into almost any form allows the machine to slice, fold, or stretch it into virtually any shape.
Stainless steel, aluminum, zinc, and copper are common sheet metals, with gauges ranging from 0.006 to 0.25 inches (0.015 to 0.635 centimetres) thick. Thick gauges are better appropriate for heavy-duty components with demanding applications, whereas thinner gauges are more flexible.
Sheet metal manufacturing may also make use of specialized equipment like band saws and chop saws. This process guarantees that the machine does the cutting evenly throughout the procedure. Cutting torches can quickly and efficiently cut vast pieces of sheet metal.
Technology made sheet metal fabrications easier by employing press brakes, which aid in creating sharp curves and angles in the metal. There are several distinct types of press brakes, each with its own set of functions and applications.
Welding is another essential aspect of sheet metal manufacturing. After it has produced all of the components, combines them and tack welds in place. Manufacturers may employ a variety of welding methods to avoid warping or other irregularities in sheet metal production. These methods include sanding the metal during the cooling phase, a unique straightening procedure, staggered welding, and the use of a strong fixture.
Sheet Metal Fabrication Process
The production line uses different fabrication methods in the sheet metal fabrication industry. The following four stages, however, are the same for all of them. We have included this process section to provide you with a better understanding of the sheet metal manufacturing process.
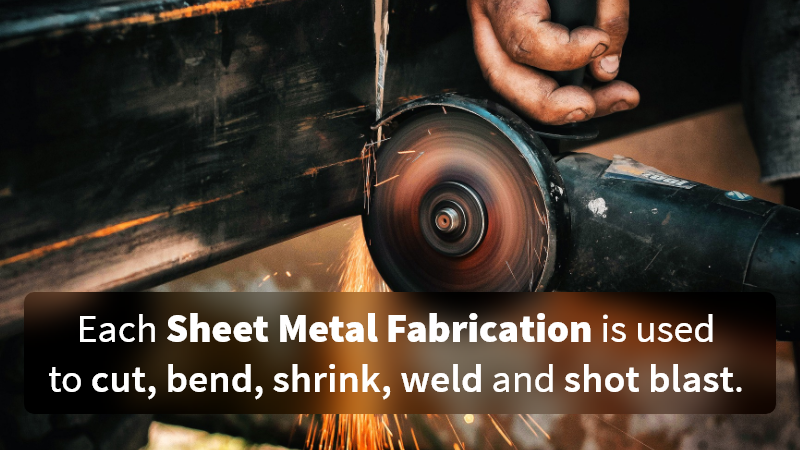
Cutting
Cutting sheet metal is one of the three primary methods of manipulating sheet metals. You may call sheet metal fabrication, like CNC machining, a subtractive manufacturing technique since it can create useable components by merely removing portions of the material.
You may cut sheet metal using various machines, some of which are specific to sheet metal production.
Laser cutting is one of the most important techniques for cutting sheet metal. A laser cutter works by focusing an intense laser via a lens. Although it may struggle with the most challenging materials, it’s a precise and energy-efficient machine that works well with thin and medium sheet metal gauges.
Water jet cutting is another option for sheet metal cutting. This cutting method is a sheet metal manufacturing technique that involves cutting the metal using a high-pressure water jet. Water jet cutters are ideal for cutting sheet metals with low melting points since they do not produce heat that might cause the metal to distort.
Plasma cutting is a third alternative for sheet metal cutting. A plasma cutter creates a hot plasma jet that quickly penetrates even thick gauges of metal sheets by creating an electrical channel of ionized gas.
Deformation
Sheet metal deformation is another vital area of sheet metal manufacturing techniques. This category of techniques includes various methods for changing and manipulating sheet metal without cutting it.
Sheet metal bending is one of the most common deformation techniques. A sheet metal business can bend sheet metal into V forms, U shapes, and channels up to 120 degrees using a brake machine. Sheet metal with a thinner gauge is simpler to bend. Decambering allows sheet metal producers to eliminate the horizontal curve from strip-shaped pieces of sheet metal.
Stamping is a kind of deformation that you may look at as a subcategory of its own. It includes using a hydraulic or mechanical stamping press with a tool and die, and it works similarly to punching, but it doesn’t permanently remove the material. Curling, sketching, embossing, flanging, and hemming are all activities you may accomplish using stamping.
Assembly
The study forms sheet metal in two ways: cutting and deformation. Assembly is a third option, which you do with or without the use of conventional fasteners.
The assembling of diverse components of sheet metal parts using fasteners such as bolts, screws, and rivets is an essential element of the entire manufacturing process, even though the study usually doesn’t consider it a fabrication process. You may use other sheet metal manufacturing techniques, such as punching,
Welding is a method of joining sheet metal components together in which the technique uses heat to melt a portion of the metal where it connects with another element. The two components’ molten metal fused to create a solid connection. Weldability is excellent in common sheet metals like stainless steel and aluminium, but various metals may weld better with different kinds of welding: arc, electron beam, resistance, and so on.
Finishing
The fabrication service may finish the product once it completes the fabrication procedure. This process usually entails polishing surfaces and edges and adds different coatings, such as powder coating.
Metal finishing is the process of applying a coating to a material to enhance its look or durability. Surface finishing is the removal of a layer from a material to improve its functioning or appearance.
Various kinds of metal fabrication finishing exist in this study. One of the most popular is anodizing, an electrochemical procedure that forms a coating of oxide on the surface of a metal component to improve its corrosion resistance. Another word to consider is metal plating, an exterior covering for a different kind of metal.
Similarly, in the industry, blackening and or coating are popular metal fabrication finishing techniques. In addition, surface finishing terminology like deburring and graining are essential in metal fabrication finishing.
Sheet Metal Fabrication Techniques
Shearing, cutting, bending, welding, shrinking, blasting, and other manufacturing techniques are only a few examples. The following are a few distinct types of fabrication methods:
Sheet Metal Shearing
Shearing is a metal manufacturing technique that removes unwanted material from sheet metal by trimming it. It entails cutting sheet metal with high accuracy using a machine or equipment, such as a bench shear. Shearing does not need the use of heat. The technique usually shears sheet metal when cool or at room temperature. It produces no waste in the form of chips, making it an appealing option for manufacturers.
Shearing is a process that involves slicing sheet metal using blade-attached equipment or tool. Shearing equipment and machines come in various shapes and sizes, with the bench shear being one of the most popular. The study also shears using guillotine machines.
Sheet Metal laser cutting
You may use the laser cutting method to cut a variety of materials, including steel and aluminium sheets, as well as three-dimensional objects like profiles and tubes.
More than two decades ago, technology launched laser cutting as an industrial technique. The study aims at a high-energy, highly focused laser beam at a workpiece during the cutting process. It produces metal vapour and melts in the process, and a high-pressure gas stream blasts them out.
However, the laser beam cuts a cutting joint or gap in the workpiece, with the cutting edge varying based on the laser beam. The technique may use a laser beam for a variety of cutting operations. The range includes cuts in metals up to 30 mm thick and very precise cutting kerfs in fragile materials. Thus, the study utilizes different lasers in CNC laser cutting, with fibre and CO2-lasers in industrial applications.
Sheet metal bending
Sheet metal bending is a common and essential process in a sheet metal fabrication factory. This technique is the plastic deformation of a piece of metal along an axis, resulting in a change in the part’s geometry. Like other metal forming processes, bending alters the shape of the workpiece while maintaining the same volume of material.
Bending can result in a slight change in sheet thickness in some cases. On the other hand, bending produces almost no change in the sheet metal thickness for the vast majority of operations. The technique uses the bending method to impart strength and stiffness to sheet metal, change the moment of inertia of a part, improve cosmetic appearance, and eliminate sharp edges, among other things.
Sheet metal welding

Welding, along with cutting, is one of the most common metal production techniques among hobbyists. Welding is the technique of connecting two distinct metal pieces. It doesn’t matter whether the components utilized in a welding application are sheets, panels, bars, or forms as long as they’re composed of metal.
You may weld using a variety of techniques and tools. The application of heat where it intends the two parts to connect is often popular to create a weld. Many metalworkers begin their careers in metal fabrication by pursuing welding jobs.
Sheet metal shrinking
It’s considerably more challenging to shrink metal than it is to extend it. Metal is pushed or squeezed into a smaller space during the shrinking process. Manufacturers employes this technique when they need to decrease the length of a piece of metal and the curve. The method shrinks in sheet metal by pounding it against a V-block or crimping it and then shrinking it.
Because a steel hammer over a hard surface stretches the metal instead of reducing it, cold shrinking necessitates the employment of both a firm surface, such as wood or steel and a soft mallet or hammer. The bigger the face of the mallet, the better.
Shot Blasting
Shot blasting is a surface preparation technique that employs a high-velocity steel abrasive. It is a technique for obtaining good cleaning and surface preparation for secondary finishing operations. Shot blasting is frequently popular for the following purposes:
- Cleaning of iron, steel, non-cast components, forgings, and other similar materials
- Sheets, rods, coils, wire, and other materials’ mechanical cleaning
- shot peening for mechanical change
Surface preparation (painting, coating, etc.) Shot blasting, in general, focuses abrasive particles at high speeds (65-110 m/s) in a controlled way at the material, eliminating surface contaminates as a result of the abrasive impact.
Summary
Sheet metal fabrication involves slicing, punching, bending, and assembling flat steel or aluminium sheets into metal structures or items. There are the most common six sheet metal fabrication techniques available in the sheet metal manufacturing world.
We have illustrated the advantages and disadvantages of all the sheet metal fabrication techniques. Thus, you can now distinguish the difference between each of the fabrication processes.
The principal attributes fabricating metals include raw materials for creating the pieces of metal necessary for the project at hand, wheel machines and saws to finish the projects and cut the metal and the original design plans made by the engineers of the original construction project. In order to protect the physical aspect of metals, sandblasting is applied.