Hydraulic and pneumatic systems find extensive applications in our daily lives. We use water in our houses, offices, or shopping malls, which require an organized water management system. Consequently, we need hydraulic systems to operate heavy machinery or private cars. Pneumatic systems can be found in HVAC systems, gas-operated manufacturing equipment, and many more. So, we can realize that these systems are indispensable. Well, control valves are the crucial components of these systems. Consequently, check valves are one of the most widely used components.
One way valves may come in various types. These types may vary based on different configurations or unique applications. Let’s explore more.
What are Check Valves?
A check valve is also famous as a one way valve. Sometimes, it may often be recognized as non-return valves. Well, they are some mechanical devices specially designed to permit the flow of fluids in one direction. It means that it prevents the backflow of fluids or gases in the opposite direction. These valves are particularly crucial for ensuring the efficiency of various fluid systems.
Let’s consider some examples. Have you ever seen how a typical water tube well works? If we disassemble, we may discover a rubber check valve between the tubewell and the pipe. It typically allows water to flow upward during pump operation. Similar applications can be found in plumbing systems. Other hydraulic systems may include water treatment plants, fire protection systems, and many more. Among the pneumatic systems, HVAC equipment, gas, and manufacturing industries are common.
How does One Way Valves Work?
As mentioned above, one way valves prevent the backflow of fluids or gases. Therefore, it needs a self-activating mechanism allowing only one-way fluid flow. This automatic functionality reduces the need for manual intervention. As a result, an operator can ensure the enhanced efficiency & reliability of fluid systems.
Moreover, this mechanism typically relies on balancing fluid pressure and the internal components. Noteworthy components include a disc, ball, or flap. These components lift or pivot as fluid or gas moves in the desired direction to permit the flow. When the fluid attempts to backflow, it automatically closes by itself. The effective sealing in the valves prevents contamination or mixing.
Types of Check Valves
Check valves typically differ in terms of design, working mechanism, and application. Each has specific qualities that distinguish it apart from the others. Operating mechanisms, design & structure, and applications are the essential aspects that distinguish them. It is sometimes determined by installation requirements, flow control, and pros & cons.
Therefore, understanding these differences helps you select the appropriate product for your project. In the following, we will talk about the 11 most popular check valves often found in many applications. For simplicity, we will mention their working principles, pros, and cons.
Type#1 Ball Check Valves
As the name implies, a ball check valve typically works by means of a ball. This ball usually moves up & down inside the valve. The seats used on these valves have a predetermined path for the ball. As a result, when there is a forward flow, the ball is pushed by the fluid against the valve seat. Consequently, it can create a seal that prevents the fluid from moving backwards.
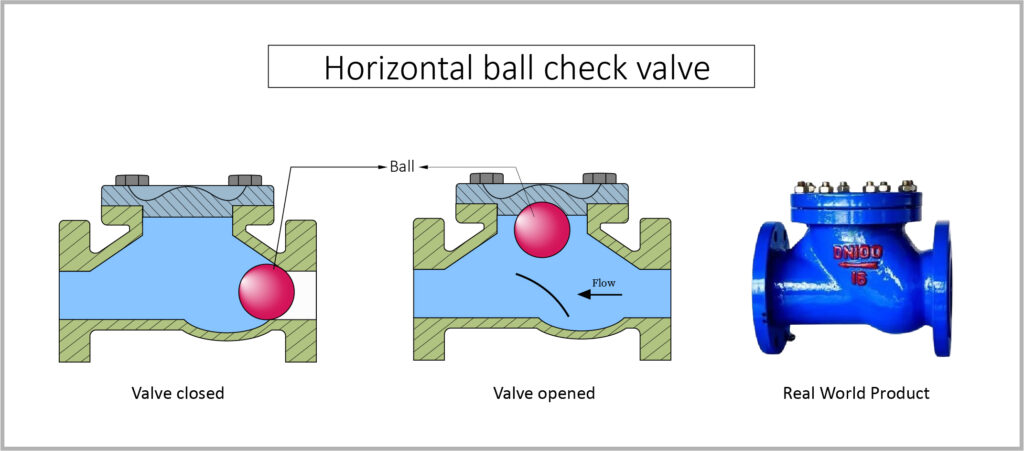
Pros
- Efficient & convenient for most use
- Requires low maintenance
- Cost-efficient solutions than other types
- Robust and suitable for low & high-pressure applications.
Cons
- Susceptible to blockages
- It may not be suitable for long-term throttling.
Type#2 Swing Check Valves
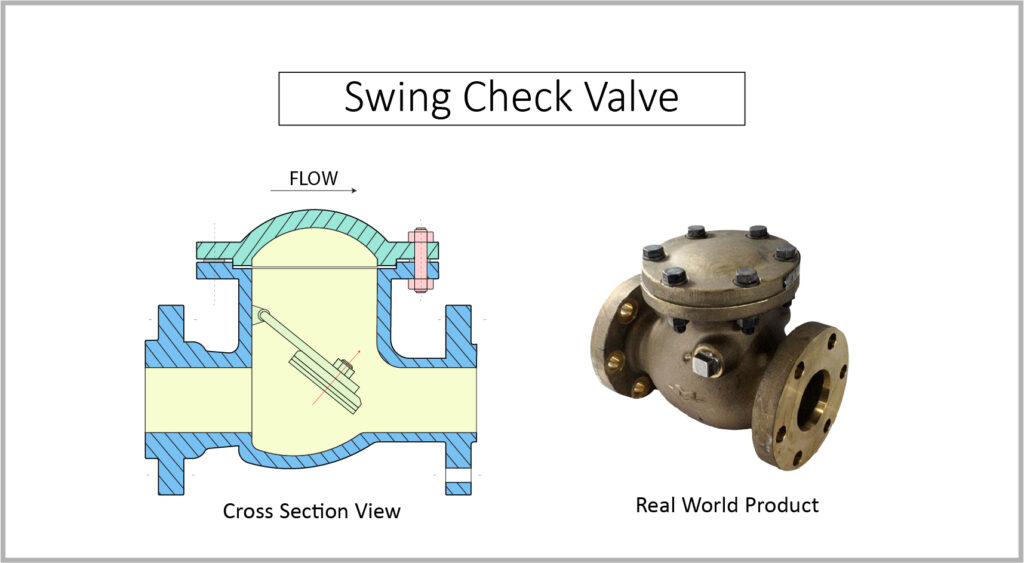
A swing check valve features a swinging disc that opens to permit flow and closes to prevent backflow. The key components of a swing check valve include the swinging disc, hinge mechanism, and body. The swinging disc is a flat or cylindrical structure. It swings on a hinge attached to the body. When the fluid flows in the correct direction, the disc swings open and allows passage. Conversely, the disc swings back to its closed position, preventing backflow.
Pros
- Low turbulence & pressure drop
- Seat rings are replaceable. Thus, they are durable and can be used for prolonged periods.
- More effortless opening of the valve, even at lower pressures
Cons
- It is not suitable for pulsating flow. Otherwise, the material flow needs to be continuous.
- It may not be suitable for high-pressure applications.
- More susceptible to cracks
Type#3 Lift Check Valves
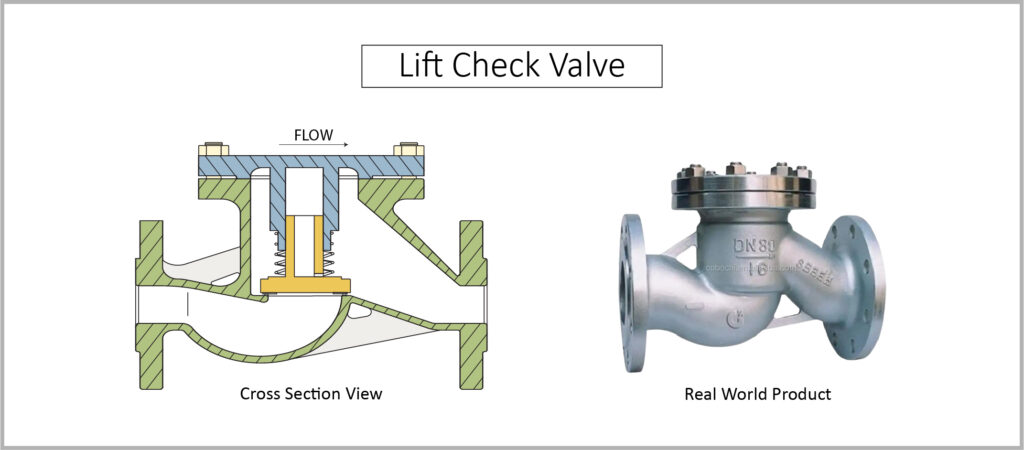
A lift check valve works through a disc or piston mechanism that lifts or moves in response to the fluid flow. In the case of forward flow, it allows the passage. Conversely, it closes to block reverse flow. The key components used in these non return valves are the movable disc or piston and the body. The disc is normally attached to a hinge or pivot within the valve. It facilitates upward movement during forward flow.
Pros
- No external moving parts
- Cost-effective & reliable
- Flexible & offers excellent controllability
Cons
- Over time, they require high energy costs.
Type#4 Butterfly Check Valves
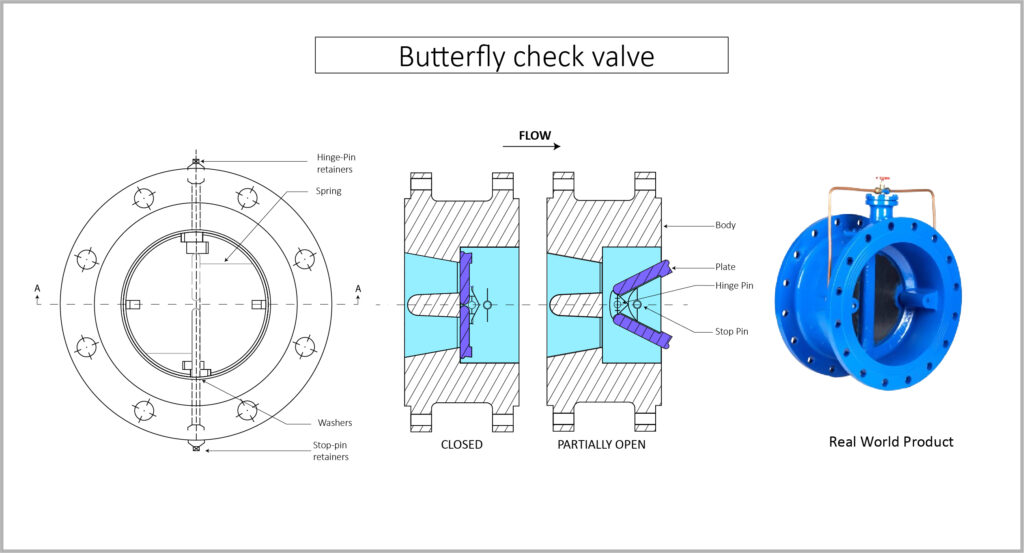
A butterfly check valve uses one of two discs to regulate the flow of fluids through a pipeline. This is the key component of butterfly check valves. They resemble the wings of a butterfly. Other key components include the valve body and a shaft that connects the disc to the actuator. The actuator can be both automatic and manual. It typically controls the rotation of the disc to enable seamless control over the direction of fluid flow.
Well, butterfly check valves may come in various types. Some popular types include wafer type, lug type, flanged type, butt weld type, and more. Note that these varieties typically are based on different uses.
Pros
- Lightweight & compact design
- Cost-effective & reliable
- Quick & Efficient
- Fluent pressure control
Cons
- Not suitable for high-pressure throttling
- Cavitation & chocked flow
Type#5 Wafer Type Check Valves
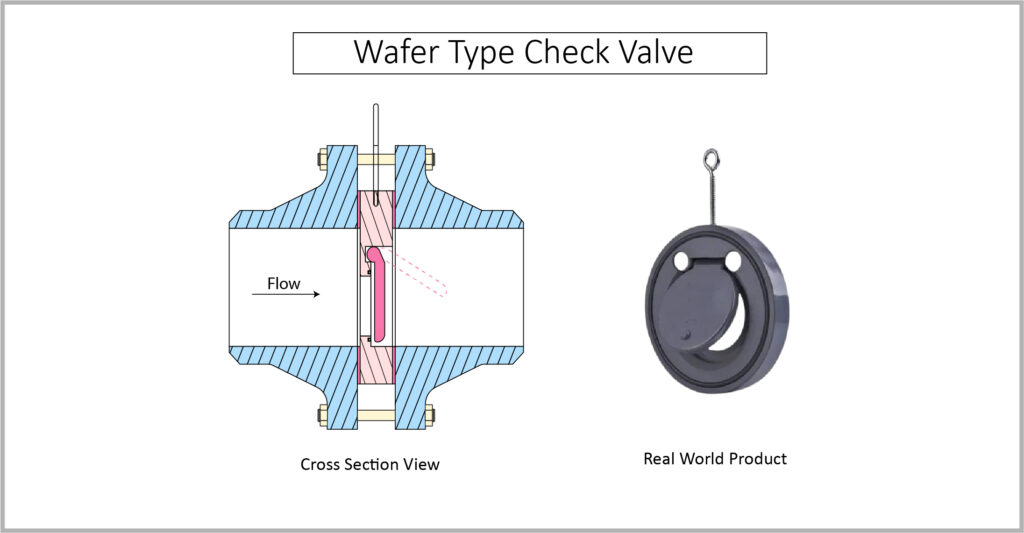
These non return valves are slim and lightweight. Wafer-type check valves are specially characterized by their wafer-thin profile. It makes them easy to install between flanges without additional gaskets. The key components of wafer type check valves include a disc and the valve body. The disc technically allows fluid to flow in one direction while preventing backflow. On the other hand, the valve is typically compact and made of materials suitable for various applications.
Pros
- High speed: They respond quickly to changes in flow direction. As a result, they are ideal for systems with high flow rates.
Cons
- It may produce noise due to rapid slamming.
- They may not provide an effective sealing. Therefore, leakage might happen in most cases.
Type#6 Tilting Disc Check Valves
Tilting disc check valves are specialized one-way valves. These valves include a disc that tilts away from the flow path when there is forward fluid pressure. Conversely, when the flow reverses, the disc returns to a closed position and prevents backflow. Other crucial components include hinge pins and the body. Hinge pins provide the pivotal movement. On the other hand, the robust valve body facilitates efficient fluid passage.
Pros
- The design can allow the pass on both sides of the disc. As a result, it offers extremely low head loss.
- Suitable for high-pressure applications
- Flexible & controllable
Cons
- They may not be suitable for wastewater applications.
- Relatively expensive than other types of one way valves
Type#7 Silent Check valves
These valves are also famous as non-slam valves. They are specialized one way valves designed to prevent water hammers that cause noise or vibrations. Silent check valves are ideal for applications where reducing the impact of flow reversal is necessary. The most common applications may include water supply systems & industrial processes.
The key components of silent check valves include a resilient hinge mechanism, a disc, and a robust body. The hinge mechanism is normally made of materials like rubber or elastomers. The silent check valve design ensures quiet operation by dampening the closing action. It reduces noise and damage related to water hammer effects.
Pros
- Reduces noise & slamming
- Ideal for clean water applications with high-head
Cons
- Rather expensive than other types of non return valves
Type#8 Duckbill Check Valves
These one way valves come with a flexible elastomeric “duckbill” shaped slit or nozzle. It resembles the beam of a duck. It is actually the key component of a duckbill check valve. Well, it allows the valve to open under pressure and close when the pressure is removed. This nozzle is typically made of silicone or rubber for flexibility. They are lightweight and come with a compact design.
Pros
- Require no intervention to open or close
- It can operate in diverse pressure ranges.
- Low noise operation
- Cost-effective
Cons
- Limited flow control
- Since the material used is mostly elastomers, it might be an issue when using aggressive chemicals.
- Limited adjustability
Type#9 Diaphragm Check Valves
As the name implies, the key component of these one way valves is the diaphragm. It is a flexible membrane positioned within the valve body. It acts as a barrier and allows fluid to pass in one direction. Conversely, it seals tightly to prevent reverse flow. This critical components is often made of rubber or synthetic polymers. Diaphragm check valves are widely popular in applications where backflow prevention is a concern. Popular applications include wastewater treatment and industrial processes.
Pros
- These non return valves can handle high pressures & temperatures.
- Diaphragm check valves also provide excellent resilience to corrosion & abrasion.
Cons
- Limited size range
- Diaphragm check valves are not ideal for vacuum services.
Type#10 Foot Check Valves
Foot check valves are also popular as bottom valves. These one way valves are designed to be installed at the pump’s inlet. It prevents backflow and maintains prime in the suction line. The essential components of a foot check valve include the body, seat, and a hinged disc. The valve body has a threaded or flanged connection for easy installation. Well, the seat ensures a proper seal, and the hinged disc opens and closes when necessary.
Pros
- Ideal for suction lift applications
- Lightweight & compact design
- Cheaper than other types
Cons
- Limited choice of materials
- It can only be used at the end of a pump’s suction line.
Type#11 Pneumatic Check Valves
As their name suggests, these one way valves are perfect for use in pneumatic systems. Its main purpose is to let air pass through in one direction while blocking backflow. Pneumatic check valves consist of three main parts: a spring, a poppet or disc, and a body. Together, these elements control the direction of airflow.
Pros
- Energy efficient
- Suitable for high-pressure applications
- Pneumatic controls offer excellent adjustable actuation pressure.
- Fast response time
Cons
- Susceptible to air leakage
- It may generate noise during operation. Therefore, it may not be suitable for noise-sensitive places.
Expert Advice
We now realize that check valves may have diverse types with varying mechanisms. It also comes in different materials and sizes. Therefore, choosing suitable non return valves for your applications becomes challenging. To solve such problems, you need to focus on some considerations. Well, these considerations can help you make informed decisions when choosing the right product.
Tip#1 Flow Characteristics
Note that different types of check valves exhibit varying flow characteristics. For instance, ball valves offer low resistance, making them suitable for high flow rates. On the other hand, Swing valves prevent backflow in irregular flow systems.
Tip#2 Fluid Types
Some valves are designed to handle specific fluids like corrosive chemicals or slurries. Therefore, checking the compatibility of the fluid is essential.
Tip#3 Pressure considerations
Pressure conditions often determine the types of check valves. For example, butterfly valves may not be suitable for high-pressure applications. Conversely, the ball valve is often chosen for high-pressure applications. Therefore, evaluating the pressure condition is crucial while selecting the right product.
Tip#4 Non-slam characteristics
You know, if your check valves close too fast, the kinetic energy can be turned into high pressure. This condition may stress the pipes and cause high noise.
Tip#5 Balance the Cost against performance
Finally, balance the overall cost of your installation with the overall performance of the system. Investing in a high-quality check valve may incur a higher initial cost, but it ensures long-term benefits.
Leave a Reply
You must be logged in to post a comment.