Cuando se habla de forja en frío frente a forja en caliente, todos cometemos errores al entender las diferencias. En este contexto, primero debemos entender en qué consiste la forja. A continuación, en la parte final del artículo, expondremos las diferencias más comunes entre forja en frío y forja en caliente.
El proceso de forja consiste en calentar, deformar y acabar una pieza de metal. Este proceso utiliza la fuerza de un ariete que cae sobre un yunque o una prensa que encierra una pieza de metal y aprieta el componente para forjar materiales con formas a medida.
Las piezas forjadas pueden soportar grandes presiones y preservar la integridad estructural bajo tensión porque los granos de metal se realinean al calentarse y doblarse.
Qué es la forja en frío
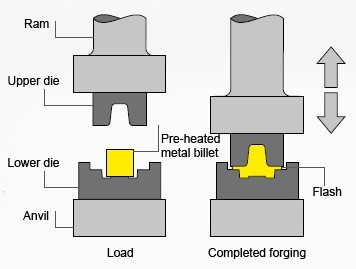
La forja en frío puede adoptar numerosas formas, como el estampado en frío, el curvado y el estirado en frío, para producir una amplia gama de artículos. El material y la forma de la matriz, el material de la pieza, el lubricante y la temperatura son aspectos esenciales del proceso de forja en frío.
Normalmente, la forja en frío se produce a temperatura ambiente o a una temperatura en la que la microestructura del metal no cambia. Es un método de compresión en el que el proceso da forma plástica a las piezas metálicas comprimiéndolas entre matrices contorneadas.
El proceso comienza con una prensa lubricada químicamente que somete la barra a presiones extremadamente altas dentro de una matriz cerrada. Después, el metal fluye y adopta la forma adecuada.
Los materiales de forja en frío pueden ir desde aleaciones de gama baja y aceros al carbono hasta aceros inoxidables de las series 300 y 400, pasando por aleaciones de aluminio seleccionadas, bronce y latón.
Aplicación de la forja en frío
Cuando el proceso necesita 10 libras o menos para forjar el peso de las piezas de forja en frío, el procedimiento es más rentable. Es prioritario cuando se trata de componentes de diseño integral, como bridas incorporadas e implantación de resaltes.
Las piezas forjadas en frío son muy populares en la fabricación del sector del automóvil para producir componentes de dirección y suspensión, sistemas de frenos antibloqueo, ejes, brocas, cubos de embrague, engranajes, piñones, pasadores, ejes de paso e intermedios y manguitos.
Proceso de forja en frío
- En primer lugar, este proceso lubrica la pieza antes de forjarla para evitar que se adhiera a la matriz y mantenerla fría durante todo el proceso de conformado, ya que la deformación puede producir temperaturas de entre 250° y 450°.
- En segundo lugar, coloque el componente metálico en un troquel que tenga la forma de la pieza final. Se puede dividir la matriz en dos partes, una unida al martillo y la otra debajo de la pieza. El martillo es el componente superior de la pieza metálica y el mecanismo de golpeo que genera la fuerza para doblarla.
- En tercer lugar, realizar el golpeo de la pieza o golpe mediante uno de estos tres mecanismos: hidráulico, neumático o mecánico. Cada técnica envía un eje con el martillo en él hacia abajo con una fuerza considerable sobre la pieza para generar la forma requerida.
- Cuarto, el Flash es un metal extra que está presente alrededor de un troquel o grupo de troqueles. Sobresale del cuerpo del forjador en forma de una fina placa en el lugar donde se unen los troqueles y durante el recorte. La rebaba restringe el flujo de metal, lo que da como resultado una impresión precisa.
- En quinto lugar, determine la forma de retirar el componente en función del tipo de procedimiento. La mayoría de las fábricas modernas emplean la automatización, como una cinta transportadora o una mano robótica, para retirar el artículo. Otra estrategia de reducción de costes elimina la necesidad de manipular el material.
- Por último, como otros aspectos del proceso, puede adoptar diversas formas. Cortar y entregar la cantidad a enviar para situaciones que necesitan sólo un troquel y un golpe. Después de que la transferencia, las partes con numerosos aspectos a diversas operaciones de troquel para la adición de características.
Ventajas e inconvenientes
Ventajas comunes
- El tratamiento previo, la temperatura y el acabado contribuyen al bajo coste de la forja en frío. Otros métodos de conformado de metales requieren algún tipo de tratamiento previo, como calentar la pieza.
- Una vez procesada una pieza en forja en frío, está completa y requiere un acabado mínimo, lo que reduce los costes de mano de obra.
- Como hay muy pocos residuos y desechos, la forja en frío puede ahorrar hasta 70% de costes de producción en términos de materiales.
- La forja en frío es un proceso sencillo que consiste en colocar la pieza directamente en la máquina de forja, que produce una pieza acabada casi al instante.
- La eliminación de las necesidades de calor es la principal razón del respeto al medio ambiente de la forja en frío, ya que los gases y el humo de los hornos provocan importantes emisiones de carbono.
- La forja en frío mejora el rendimiento de los productos reorganizando la estructura del grano de la pieza de trabajo para que coincida con la configuración de la pieza final.
- Trabajar con metal puede acarrear una serie de problemas. Al aumentar la resistencia general del metal y minimizar la posibilidad de pérdida de integridad del material, el forjado en frío evita algunos de los efectos negativos, como la fatiga por porosidad.
- Las piezas forjadas en frío pueden soportar mucha presión. La pieza puede mantener su forma revisada incluso cuando se la empuja más allá de su límite elástico o de fluencia.
Otras ventajas
- A lo largo de una tirada de fabricación, mantiene las tolerancias críticas y estrechas de las piezas. Han recreado meticulosamente hasta el punto de que cada componente es una réplica idéntica del original.
- La forja en frío, a diferencia de otros procedimientos, ofrece flexibilidad creativa y permite crear curvas y formas complicadas que, de otro modo, necesitarían varios métodos secundarios distintos y costosos.
- La forja en frío, a diferencia de otros procedimientos, ofrece flexibilidad creativa y permite crear curvas y formas complicadas que, de otro modo, necesitarían varios métodos secundarios distintos y costosos.
- Aunque existen diferencias en los procesos de producción de la forja en frío, la alta velocidad de fabricación de la forja en frío puede crear hasta 400 piezas por minuto. El único factor que afecta a la velocidad del proceso es el tamaño de la pieza.
- La forja es posible con diversos metales, incluidos metales duros como el acero al carbono, el acero aleado y el acero inoxidable, y metales blandos como el aluminio, el latón y el cobre.
Desventajas
- La forja en frío no es perfecta. Como cualquier proceso de producción, la forja en frío tiene límites e inconvenientes que deberá examinar antes de adoptarla para su próximo proyecto de producción.
- Sólo se pueden fabricar formas y patrones primarios en grandes cantidades. No se pueden hacer diseños únicos o complicados mediante forja en frío. Los niveles de deformación y los grados de conformado están restringidos, y los metales forjados en frío tienen una flexibilidad reducida.
- El cambio de la estructura del grano del metal le ofrece mayor resistencia, pero puede provocar tensiones residuales.
- Ciertos tipos de forja en frío necesitan tratamientos térmicos para eliminar cualquier fractura o endurecimiento por fluencia.
- Los metales que pueden forjarse en frío están limitados. No debe seleccionar los que tengan poca plasticidad y susceptibilidad a la tensión para endurecerlos, ya que pierden su elasticidad y se romperán bajo tensión de tracción. Sólo se pueden utilizar metales que tengan una dureza de HRC 44 en la escala Rockwell.
- Las operaciones de producción necesitan una cantidad considerable de fuerza para proporcionar la resistencia a la compresión y la presión necesarias. Aunque la inclusión de la hidráulica y la neumática ha reducido el tamaño de los equipos, no ha eliminado la cantidad de potencia que utilizan las máquinas.
- Las herramientas, las matrices y los moldes deben estar cuidadosamente desarrollados, ser duraderos y lo suficientemente potentes como para soportar una tensión repetitiva continua.
Qué es la forja en caliente
Calentar el metal por encima de su temperatura de recristalización para la forja en caliente. Este proceso reduce la tensión de flujo y la energía necesarias para producir el metal, lo que permite aumentar el ritmo de producción (o velocidad de deformación). La forja en caliente simplifica la conformación del metal y lo hace menos propenso a la fractura.
Las temperaturas estándar para la forja en caliente incluyen: Aleaciones de aluminio (Al) - 360° (680°F) a 520°C (968°F); Aleaciones de cobre (Cu) - 700°C (1 292°F) - 800°C (1 472°F); Acero - hasta 1 150°C (2 102°F).
Aplicación de la forja en caliente
Normalmente, la forja Ho utiliza altas temperaturas en el proceso de recristalización. Este método mejora la conformabilidad y permite ajustar la microestructura de grano fino. La forja en caliente, más que cualquier otro método de conformado, es conocida por su enorme resistencia y longevidad.
También permitirá la forja en caliente en situaciones en las que las elevadas cargas operativas requieran componentes especializados. Estas piezas pueden denominarse "piezas críticas para la seguridad". Las industrias automovilística y aeroespacial son los principales compradores de piezas forjadas en caliente.
Proceso de forja en caliente
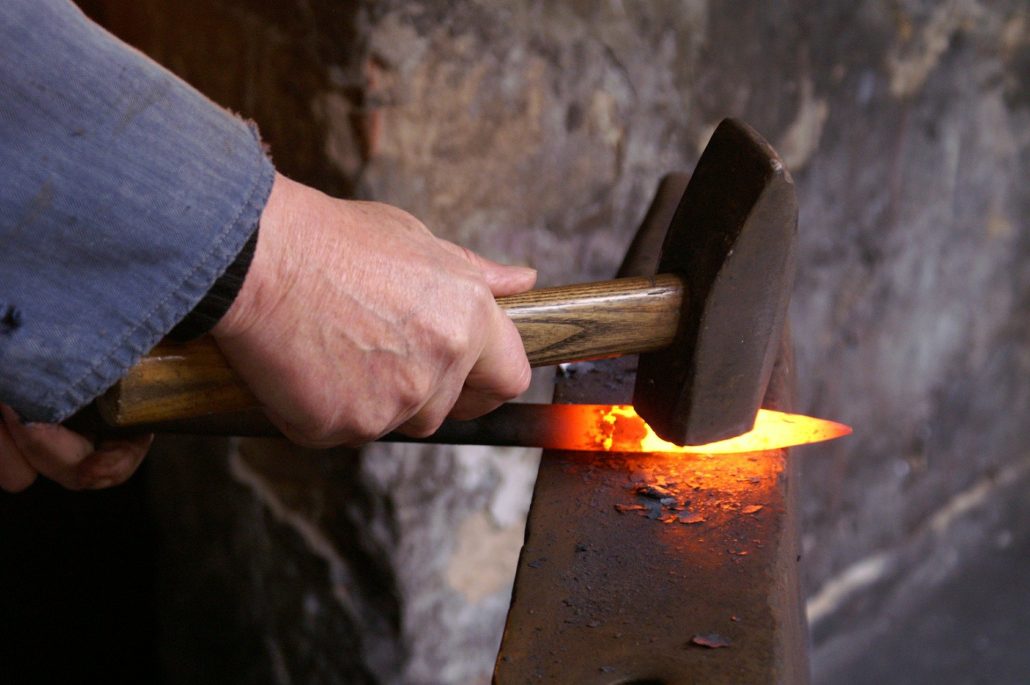
En primer lugar, llevar a cabo el proceso de forja en caliente a la temperatura más significativa posible sin destruir las propiedades metalúrgicas de la aleación (hasta 1250 °C para el acero, de 300 a 460 °C para las aleaciones de aluminio, de 750 a 1040 °C para las aleaciones de titanio y de 700 a 800 °C para las aleaciones de cobre).
En segundo lugar, la recristalización se produce al mismo tiempo que la deformación, lo que elimina el endurecimiento por deformación. Por consiguiente, y para obtener resultados óptimos, la temperatura de forja debe mantenerse por encima de un determinado mínimo durante toda la operación, en función de la aleación.
Esta condición también elimina la posibilidad de que la falta de ejecutabilidad provoque fracturas, ya que disminuye la flexibilidad a temperaturas más bajas. Después de la sincronización, El procedimiento de forja se mantiene por debajo de estas restricciones de temperatura.
En cuarto lugar, si el proceso no termina de forjarse cuando alcanza el límite inferior, es necesario recalentarlo si es posible. En caso contrario, hay que tratar el artículo como forjado y acabarlo de otra manera. Dado que el intervalo de temperatura necesario para el proceso de forja en caliente es tan crítico, todos los utillajes se calientan para evitar que el componente pierda temperatura durante la etapa de forja.
Este método dio lugar a una tecnología de forja en matriz cerrada exacta y precisa conocida como "forja isotérmica".
Quinto, seguir calentando las herramientas (en realidad las matrices) a la temperatura de forja deseada durante la forja isotérmica. Sin embargo, en función del material y, por tanto, de la temperatura de forja, esta noción se aplica de distintas maneras. El material de la matriz debe mantener las elevadas características mecánicas necesarias para deformar el material del componente a la temperatura de forja.
En sexto lugar, el proceso isotérmico puede variar de un material a otro, por ejemplo:
- Dado que el aluminio se enfría rápidamente y la temperatura de forja es baja, es imprescindible para la forja del aluminio: todas las calidades de las matrices deben mantener las cualidades mecánicas requeridas.
- Se puede conseguir para aleaciones de cobre y titanio si las matrices son de una calidad sofisticada (y costosa).
- Para las aleaciones de acero, donde muy pocos materiales mueren para mantenerse a 1250 °C de tensión de forja, es todo un reto.
En consecuencia, la forja isotérmica es poco común para las aleaciones de titanio. Y muy reservada para el acero y las aleaciones a base de níquel (dedicadas, por ejemplo, a los discos de turbina más difíciles para motores a reacción).
Ventajas e inconvenientes
Ventajas
- La principal ventaja de la forja en caliente es que el proceso de recristalización elimina los efectos de endurecimiento por deformación cuando se deforma el metal.
- Las piezas tienen mayor elasticidad, lo que las hace adecuadas para una amplia gama de aplicaciones.
- Estructura granular con homogeneización
- La falta de porosidad permite una gran variedad de procedimientos de acabado, como el pulido y el tratamiento de superficies.
- Cuando se trata de metales más estrictos, como el acero, se trata de una técnica eficaz.
Desventajas
- Las tolerancias son menos exactas.
- Es posible que el material se deforme durante el proceso de enfriamiento.
- La estructura del grano del metal varía.
- Posibles interacciones entre el metal y el medio ambiente (formación de incrustaciones)
Forja en frío frente a forja en caliente
La forja en frío frente a la forja en caliente es un tema muy importante de debate hoy en día. La contribución de estos dos procesos es enorme. La diferencia de temperatura entre la forja en caliente y en frío es diferente. La forja en frío somete a tensiones y deformaciones los metales a temperatura ambiente. Por otro lado, la forja en caliente calienta los metales cerca o a su temperatura de fusión.
La recristalización es la clave del intervalo de temperaturas. La forja en frío se produce antes de la recristalización, mientras que la forja en caliente se produce después de la recristalización.
La decisión entre forja en frío y en caliente se basa en los siguientes factores:
- Equipos de fabricación y mecanizado: Para sacar el máximo partido a sus equipos, los productores se especializan en una u otra técnica.
- La demanda de los clientes: Los ingenieros deciden el procedimiento óptimo para generar sus ideas durante la fase de diseño de la creación de componentes.
- Tipos de componentes producidos: El diseño del componente suele determinar las limitaciones a la hora de seleccionar la técnica adecuada, ya que determinadas piezas sólo pueden forjarse en caliente. En cambio, otras son ideales para la forja en frío. Los componentes forjados en frío tienen diseños básicos con pocos detalles complicados, pero los miembros forjados en caliente pueden tener elementos diminutos microscópicos increíblemente exactos.
Los fabricantes prefieren la forja en frío siempre que sea posible, ya que necesita menos equipamiento y no incluye el calentamiento, lo que reduce sustancialmente los costes de fabricación.
Resumen
El proceso de forja consiste en calentar, deformar y acabar una pieza de metal. Hay dos tipos: forja en frío y forja en caliente.
La forja en frío puede adoptar numerosas formas, como el estampado en frío, el doblado y el estirado en frío, para producir una amplia gama de artículos. Por otro lado, la forja en caliente se produce calentando el metal por encima de su temperatura de recristalización para forjarlo en caliente.
Hemos expuesto las diferencias comunes entre los procesos de forja en frío y forja en caliente. Esperamos haber podido mencionar las diferencias específicas entre ellos.