Fundición de metales es una técnica contemporánea con una larga historia. Diversas formas metálicas se obtienen mediante el proceso de fundición de metales vertiendo metal fundido en la cavidad de un molde, donde se enfría antes de ser extraído del molde. Sin embargo, el proceso de fundición a la cera perdida es uno de los procesos de fundición de metales más populares en la industria manufacturera.
¿Qué es la fundición a cera perdida?
El proceso de fundición a la cera perdida se conoce a veces como fundición a la cera perdida. Hace miles de años, la humanidad vertía metal fundido en un molde de cerámica desechable, convirtiendo la fundición a la cera perdida en uno de los primeros métodos industriales.
Las piezas moldeadas a la cera perdida de acero inoxidable son productos de fundición a la cera perdida de uso cotidiano que llevan incorporada una capa de óxido de cromo que les confiere unas cualidades anticorrosivas superiores, a diferencia de otros materiales. Las piezas de acero inoxidable son útiles para aplicaciones militares, médicas e industriales por su resistencia a la corrosión.
La fundición a la cera perdida crea componentes exactos con la menor cantidad de residuos, energía y mecanizado posterior. También puede garantizar la fabricación de piezas muy complejas. Para los ingenieros de diseño, este escenario hace que la técnica de fundición a la cera perdida sea extremadamente útil.
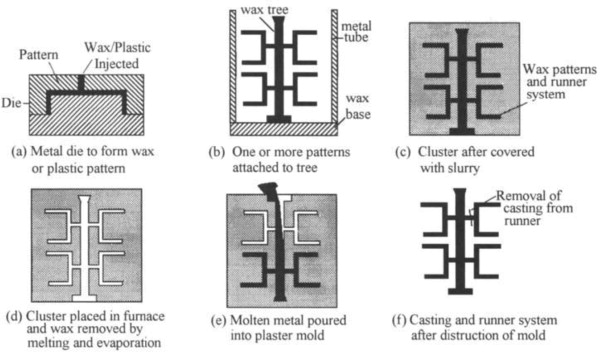
Proceso de fundición a la cera perdida
El proceso de fundición a la cera perdida requiere el uso de una matriz metálica, cera, cerámica, lechada, horno, metal fundido y cualquier máquina que necesite chorro de arena, corte o esmerilado.
A continuación se describe paso a paso el proceso de fabricación de diversas formas metálicas.
Primer paso: patronaje
Un fabricante de moldes profesional o artistas escultores hacen un patrón maestro de cera, arcilla, madera, acero o plástico, en función de las especificaciones del producto final.
Considera la tolerancia de contracción para la forma generada de cera y material de fundición el nombre de "patrón maestro" para la tolerancia de contracción doble. Emplea un patrón con características idénticas a las del objeto acabado, excepto un margen de dilatación térmica.
Los diseños de cera suelen moldearse por inyección en una matriz metálica y producirse como una sola pieza. En este caso, puede utilizar los núcleos para crear cualquier característica interna del patrón.
Dependiendo del tamaño, la forma y el material utilizado, este método puede requerir cierto ensayo y error para conseguir el tamaño y la forma perfectos, lo que hace que estos moldes sean caros.
Un sistema central de inyección de cera conecta varios diseños para producir un ensamblaje en forma de árbol en esta fase (bebedero, canales y bandas). El sistema de inyección crea caminos para que el metal fundido se desplace a través de su aproximación a la cavidad del molde.
Segundo paso: Creación del molde
El artista de la fabricación hace del troquel maestro un molde que se adapta al patrón maestro. Si el patrón maestro construido es de acero, el troquel maestro podría fundirse directamente a partir del diseño utilizando un metal con un punto de fusión más bajo.
También puede fundir los moldes de caucho a partir del patrón maestro. Como alternativa, puede fabricar un molde maestro sin necesidad de un patrón maestro.
Tercer paso: Producción del patrón de cera
Aunque el uso de diseños de cera es habitual, también se pueden utilizar otros materiales, como plástico y mercurio congelado. Existen dos métodos para crear diseños de cera.
En uno de los métodos, puede verter la cera en el molde y agitar hasta que una capa uniforme, normalmente de 3 mm (0,12 pulgadas) de espesor, cubra la superficie interior del molde. Este procedimiento continúa hasta que aparece el grosor de patrón requerido.
Otro método consiste en llenar todo el molde con cera fundida y dejar que se solidifique.
Si necesita un núcleo, dispone de dos alternativas: cera soluble o cerámica. Pretende que los núcleos de cera soluble se fundan fuera del revestimiento con el resto del patrón de cera, mientras que elimina los cuerpos cerámicos una vez que el objeto se haya solidificado.
Paso 4: Montaje de los patrones de cera
Puede generar múltiples diseños de cera e integrarlos en un único diseño colosal. Realiza el colado en un único colado por lotes. Esta etapa une los patrones a un bebedero de cera para formar un grupo de patrones o árbol en este caso.
Necesitará una herramienta de calentamiento para fundir suavemente superficies de cera específicas, que luego se colocan unas contra otras y se dejan enfriar y reafirmar para unir los patrones.
Haz un árbol de hasta varios cientos de motivos. También puedes realizar diseños en cera, que consisten en frotar las líneas de separación o los destellos con un instrumento metálico caliente. Por último, viste los motivos para que parezcan artículos acabados.
Paso 5: Aplicación de los materiales de inversión
El molde cerámico, también conocido como revestimiento, se fabrica repitiendo una serie de pasos de recubrimiento, estucado y endurecimiento hasta que alcanza el grosor necesario.
El revestimiento consiste en sumergir un grupo de moldes en una lechada fina de material refractario y escurrirla a continuación para generar un revestimiento homogéneo de la superficie. Los materiales delicados, a menudo conocidos como capas de imprimación, conservan buenas características del molde en esta primera fase.
El estucado incorpora partículas cerámicas gruesas a los diseños sumergiéndolas en un lecho fluidizado, lijándolas con una lijadora en húmedo o aplicando los materiales a mano. Los revestimientos pueden curarse tras endurecerse. Este proceso continúa hasta que el revestimiento alcanza el grosor deseado.
Deje que los moldes de revestimiento se sequen por completo, lo que puede llevar entre 16 y 48 horas. Acelere el secado utilizando el vacío o reduciendo la humedad ambiental. También puede hacer moldes de revestimiento colocando grupos de patrones en un matraz y vertiendo material de revestimiento líquido desde arriba.
IT hace vibrar el matraz para que salga el aire atrapado y ayuda al material de revestimiento a rellenar los pequeños espacios.
La sílice, el circón, los silicatos de aluminio y la alúmina son materiales refractarios habituales en la fabricación de revestimientos. A menudo utiliza sílice en forma de sílice fundida. Sin embargo, en ocasiones utiliza cuarzo por ser menos costoso.
Los silicatos de aluminio combinan alúmina y sílice con un porcentaje de alúmina que oscila entre el 42 y el 72 por ciento; con un 72 por ciento de alúmina, podemos denominarlo mullita. Suele utilizar refractarios a base de circonio durante la(s) capa(s) primaria(s) porque es menos probable que el circonio reaccione con el metal fundido.
Antes de utilizar sílice, utiliza una mezcla de yeso y moldes viejos triturados (chamota). Paráfrasis formalizada Entre los aglutinantes utilizados para mantener el material refractario en su sitio se encuentran el silicato de etilo, la sílice coloidal, el silicato de sodio y un híbrido de éstos con pH y viscosidad regulados.
Sexto paso: Dewax
Dé la vuelta a los moldes de cerámica y colóquelos en un horno o autoclave para fundir y evaporar la cera. Provoca la mayor parte de los fallos del revestimiento por resinas con un coeficiente de dilatación térmica significativamente mayor que el material de revestimiento que las rodea.
Cuando funde la cera, se expande y provoca tensiones. Caliente la cera lo antes posible para reducir estas tensiones, permitiendo que las superficies exteriores de cera se fundan y escurran rápidamente, dejando que la mayor parte de la resina se expanda.
En algunos casos, taladre los agujeros en el molde antes de calentarlo. Puede recoger y reutilizar la cera que se escape del molde.
Paso 7: precalentamiento
Exponer el molde al quemado, que calienta el molde a temperaturas que oscilan entre 870 °C y 1095 °C para eliminar la humedad y los restos de cera y sinterizar el molde.
Después, utilice este calentamiento para preparar el molde antes de verterlo. Mientras tanto, Deje que el molde se enfríe antes de ser probado.
El precalentamiento permite que el metal permanezca líquido durante más tiempo, lo que permite un llenado más excelente de todas las características del molde y una mayor precisión dimensional. Después de que el molde se haya enfriado, puede arreglar cualquier defecto descubierto con lechada cerámica o cemento específico.
Paso 8: Verter
A continuación, el molde de revestimiento se coloca abierto hacia arriba en un recipiente lleno de arena. El metal puede verterse por gravedad o mediante presión positiva de aire u otras presiones.
Utilice fuerzas adicionales en el vaciado al vacío, el vaciado por inclinación, el vaciado asistido por presión y el vaciado centrífugo, que son especialmente eficaces cuando los moldes tienen piezas delicadas que, de otro modo, serían difíciles de llenar.
Noveno paso: Desinversión
Martillear la carcasa, chorrearla con medios abrasivos, hacerla vibrar, chorrearla con agua o disolverla químicamente (a menudo con nitrógeno líquido). Retirar y reciclar el bebedero. Y, a continuación, limpiar la pieza fundida para eliminar cualquier rastro del proceso de fundición, lo que suele hacerse mediante esmerilado.
Décimo paso: Acabado
Somete la pieza de fundición acabada a un proceso de acabado tras su rectificado. Elimina las impurezas y los negativos utilizando herramientas manuales y soldadura, lo que supone un paso más allá del rectificado. Si el artículo requiere un enderezado adicional, utiliza prensas enderezadoras hidráulicas para ajustar el producto a sus tolerancias.
Aplicación del proceso de fundición a la cera perdida
La fundición a la cera perdida es una de las primeras tecnologías de fundición, y es un monumento a su uso que pueden utilizar muchas empresas comerciales e industriales en la actualidad.
A continuación se enumeran sólo algunas de las aplicaciones más populares y esenciales de la fundición a cera perdida:
- En motores y generadores, componentes de ingeniería como rotores y álabes de turbina.
- Componentes de válvulas (carcasas, pistones, etc.)
- Fabricación de armas de fuego (gatillos, martillos, etc.)
- Equipos de fabricación para la industria alimentaria y de bebidas
- Con un uso tan amplio, es razonable concluir que la inversión en herramientas y equipos de fundición ha ayudado prácticamente a todas las industrias.
Proveedores populares de fundición a cera perdida
La fundición a presión es un buen negocio hoy en día para los talleres metalúrgicos. En EE.UU. hay un buen número de proveedores de fundición a la cera perdida.
Según la demanda del mercado de 2024, los famosos proveedores de fundición a presión son Precision Castparts Corp., Alcoa Corporation, Impor Industries USA, Inc., metalTek Internacional, Sigma OEM.
Resumen rápido de la fundición a la cera perdida frente a la fundición en arena Fundición en arena
La fundición a la cera perdida es a veces bastante más cara que la fundición en arena, debido a la complejidad y la preparación necesarias.
La calidad de la superficie del producto final es otra distinción crítica entre el moldeo a la cera perdida y el moldeo en arena. Para obtener el resultado final de un molde de fundición en arena, lo mejor es romperlo. Como resultado de las líneas de separación en el molde, las piezas terminadas tienen una costura. La arena, algo gruesa, también deja una superficie igualmente rugosa en las piezas fundidas.
En la fundición a la cera perdida, en cambio, se emplean moldes cerámicos complejos. Las piezas acabadas presentan superficies lisas, tolerancias estrechas y paredes finas. Las piezas de fundición no suelen necesitar ningún tratamiento adicional tras retirar las compuertas y los bebederos.
Dado que la fundición a la cera perdida emplea lechada líquida para producir los moldes, los componentes fundidos pueden tener prácticamente cualquier forma, lo que permite a los ingenieros incluir detalles intrincados y geometrías complicadas en sus diseños. Con frecuencia, las piezas fundidas en arena se estrechan (con ángulos de desmoldeo) o se contornean para que puedan emerger con facilidad y suavidad de la arena compactada.
La fundición en arena tiene la ventaja de que es relativamente fácil cambiar el molde para adaptarlo a las modificaciones del diseño. En el caso de las versiones de cera, es posible que los técnicos tengan que modificar o sustituir el patrón de metal sólido o crear nuevos moldes, lo que puede resultar un procedimiento más complicado con la fundición a la cera perdida.
Ventajas y desventajas del proceso de fundición a la cera perdida
La fundición a la cera perdida, como cualquier otra tecnología de producción, no es perfecta. Dependiendo de la forma de su modelo, puede que no sea una metodología adecuada, o simplemente puede ser demasiado lenta para el rendimiento previsto. Éstas son las ventajas e inconvenientes que hay que tener en cuenta a la hora de elegir entre la fundición a la cera perdida y otros métodos alternativos:
Ventajas
Capaz de reproducir diseños complejos
Producir modelos de gran precisión, incluso con características diminutas y paredes finas, es una de las razones clave por las que la fundición a la cera perdida suele ser el proceso de fabricación preferido.
El grado de detalle de la fundición a la cera perdida es suficiente para las empresas que dependen de equipos y componentes de alta precisión, como los automóviles y los aviones.
Incluso los joyeros con visión de futuro han empezado a ver las ventajas de la fundición a la cera perdida.
Las coladas tienen superficies lisas después de salir
Las piezas de metal fundido que salen del molde tienen superficies increíblemente lisas gracias a que el molde se fabrica rodeando el diseño maestro con una lechada de material refractario.
Requerirá cierto tratamiento posterior para que los moldes metálicos queden precisamente impecables, pero llevará bastante menos tiempo y esfuerzo.
La precisión dimensional es excelente
Los materiales refractarios para el molde en la fundición a la cera perdida ayudan a conservar las proporciones originales del modelo maestro. Cuando se somete al calor, esta estabilidad dimensional se traduce en piezas de metal fundido que, a escala, son fieles al modelo original.
La fundición a la cera perdida puede alcanzar tolerancias de hasta 0,076 milímetros, según los especialistas.
Desventajas
Los ciclos de producción son más largos
Aunque algunos elementos del proceso de fundición a la cera perdida pueden ser automáticos, sigue siendo mucho más lento que otros procesos de producción. La fundición a la cera perdida puede suponer un dilema para las industrias que dependen de un alto volumen de producción y una rápida rotación.
Caro
Aunque el proceso de fundición a la cera perdida parece sencillo, es un procedimiento caro debido al elevado coste de los materiales y el equipo especial. En este caso, hay mucho trabajo físico implicado, también debe considerar el coste de entrega.
Si te dedicas a la producción a pequeña escala, es posible que la inversión en fundición no resulte rentable.
No recomendado para diseños con núcleos
Puede utilizar el moldeo a la cera perdida para fabricar cosas increíbles, como álabes de turbina o carcasas de bomba. Sin embargo, si la forma de su modelo tiene un núcleo hueco, es posible que tenga que investigar formas alternativas más apropiadas.
Resumen
El proceso de fundición a la cera perdida es un proceso de fundición de metales muy popular en todo el mundo. A partir de lo expuesto anteriormente, hemos descrito el proceso de fundición a la cera perdida paso a paso. Esperamos que sea lo suficientemente claro para entender cada uno de los procesos de fundición mencionados.
Sin embargo, la fundición a la cera perdida es un método beneficioso y excelente para la fundición de metales. Pero también tiene algunas consideraciones. En ese caso, tiene algunos pros y contras. También los hemos descrito.
Además, también hemos demostrado la aplicación de la fundición a la cera perdida, la fundición a la cera perdida frente a la fundición en arena, y el famoso proveedor de fundición a la cera perdida en EE.UU.