Fundição de metal é uma técnica contemporânea com uma longa história. Várias formas de metal são obtidas por meio do processo de fundição de metal, despejando metal fundido em uma cavidade do molde, onde ele esfria antes de ser retirado do molde. No entanto, o processo de fundição por cera perdida é um dos processos mais populares de fundição de metal no setor de manufatura.
O que é fundição por cera perdida?
O processo de fundição por cera perdida também é conhecido como fundição por cera perdida. Há milhares de anos, a humanidade derramou metal fundido em um molde de cerâmica descartável, tornando a fundição por cera perdida um dos primeiros métodos industriais.
As peças fundidas de aço inoxidável são produtos de fundição de investimento comuns que têm uma camada de óxido de cromo incorporada que proporciona qualidades anticorrosivas superiores, ao contrário de outros materiais. As peças fundidas de aço inoxidável são úteis para aplicações militares, medicinais e industriais devido à sua resistência à corrosão.
A fundição por cera perdida cria componentes exatos com o mínimo de desperdício, energia e usinagem subsequente. Ela também pode garantir a fabricação de peças altamente complexas. Para os engenheiros de projeto, esse cenário torna a técnica de fundição por cera perdida extremamente útil.
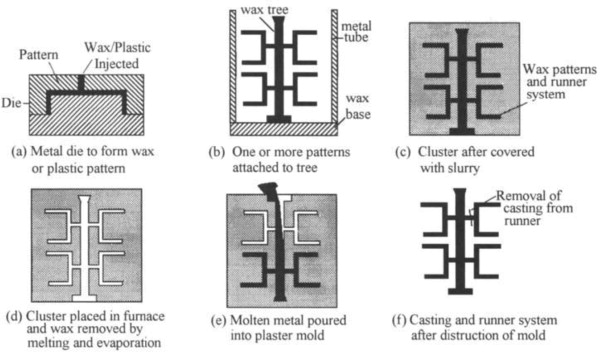
Processo de fundição por cera perdida
O processo de fundição de revestimento requer o uso de uma matriz de metal, cera, cerâmica, lama, forno, metal fundido e qualquer máquina que precise de jateamento de areia, corte ou esmerilhamento.
A seguir, o processo passo a passo pelo qual as pessoas fazem várias formas de metal.
Primeira etapa: criação de padrões
Um fabricante de moldes profissional ou artistas de escultura fazem um padrão mestre de cera, argila, madeira, aço ou plástico, dependendo das especificações do produto final.
Ele considera a tolerância de encolhimento para a forma gerada de cera e material de fundição, o nome \"padrão mestre\" para a tolerância de encolhimento dupla. Ele emprega um padrão com características idênticas às do objeto acabado, exceto uma tolerância de expansão térmica.
Os designs de cera geralmente são moldados por injeção em uma matriz de metal e produzidos como uma única peça. Nesse caso, você pode usar os núcleos para criar qualquer recurso de padrão interno.
Dependendo do tamanho, da forma e do material usado, esse método pode exigir algumas tentativas e erros para obter o tamanho e a forma perfeitos, o que torna esses moldes caros.
Um sistema central de passagem de cera conecta vários projetos para produzir um conjunto semelhante a uma árvore nesse estágio (jito, canais e risers). O sistema de canais cria caminhos para o metal fundido percorrer em sua aproximação da cavidade do molde.
Segunda etapa: Criação do molde
O artista de fabricação faz do molde mestre um molde adequado ao padrão mestre. Se o padrão mestre construído for de aço, o molde mestre poderá ser fundido diretamente do projeto usando um metal de ponto de fusão mais baixo.
Você também pode fundir os moldes de borracha a partir do padrão mestre. Como alternativa, você pode fabricar um molde mestre sem a necessidade de um padrão mestre.
Terceira etapa: Produção do padrão de cera
Embora o uso de desenhos de cera seja comum, você também pode usar outros materiais, como plástico e mercúrio congelado. Há dois métodos para criar padrões de cera.
Em um dos métodos, você pode derramar a cera no molde e agitar até que uma camada uniforme, normalmente de 3 mm (0,12 pol.) de espessura, cubra a superfície interna do molde. Esse procedimento continua até que a espessura necessária do padrão apareça.
Outra abordagem inclui o preenchimento de todo o molde com cera derretida e a sua solidificação.
Se você precisar de um núcleo, há duas alternativas disponíveis: cera solúvel ou cerâmica. O objetivo é que os núcleos de cera solúvel derretam do revestimento de revestimento com o restante do padrão de cera, ao passo que os corpos de cerâmica são removidos após a solidificação do objeto.
Quarta etapa: Montagem dos padrões de cera
Você pode gerar vários designs de cera e integrá-los em um único design colossal. Ele é fundido em um único lote de vazamento. Esse estágio une os padrões a um jito de cera para formar um conjunto de padrões ou uma árvore, nesse caso.
Você precisará de uma ferramenta de aquecimento para derreter suavemente superfícies específicas de cera, que são então colocadas umas contra as outras e deixadas esfriar e firmar para unir os padrões.
Faça uma árvore com até várias centenas de motivos. Você também pode fazer desenhos com cera, que envolvem esfregar as linhas de separação ou os brilhos com um instrumento de metal quente. Por fim, vista os padrões para que se assemelhem a itens acabados.
Quinta etapa: Aplicação dos materiais de investimento
O molde de cerâmica, também conhecido como revestimento, é feito por meio da repetição de uma série de etapas - revestimento, estuque e endurecimento - até atingir a espessura necessária.
O revestimento envolve a imersão de um conjunto de moldes em uma pasta de material refratário fino e, em seguida, a drenagem para gerar um revestimento de superfície homogêneo. Materiais delicados, geralmente conhecidos como revestimentos primários, retêm boas características do molde nessa primeira fase.
O estuque incorpora partículas grossas de cerâmica aos projetos, mergulhando-as em um leito fluidizado, lixando-as com uma lixadeira úmida ou aplicando os materiais manualmente. Os revestimentos podem ser curados após o endurecimento. Esse processo continua até que o revestimento atinja a espessura desejada.
Permita que os moldes de revestimento curem completamente, o que pode levar de 16 a 48 horas. Acelere a secagem usando vácuo ou reduzindo a umidade ambiente. Você também pode fazer moldes de revestimento organizando clusters de padrões em um frasco e, em seguida, despejando material de revestimento líquido por cima.
O IT vibra o frasco para permitir que o ar preso saia e ajude o material de revestimento a preencher os pequenos espaços.
Sílica, zircônio, silicatos de alumínio e alumina são materiais refratários comuns usados para fazer investimentos. Geralmente utiliza sílica na forma de sílica fundida. No entanto, ocasionalmente utiliza quartzo, por ser menos dispendioso.
Os silicatos de alumínio combinam alumina e sílica com uma porcentagem de alumina que varia de 42% a 72%; com 72% de alumina, podemos chamar isso de mulita. Normalmente, a empresa usa refratários à base de zircônio durante as camadas primárias porque o zircônio tem menos probabilidade de reagir com o metal fundido.
Antes de usar a sílica, ela utiliza uma mistura de gesso e moldes antigos triturados (chamotte). Os aglutinantes usados para manter o material refratário no lugar incluem silicato de etila, sílica coloidal, silicato de sódio e um híbrido desses que tem o pH e a viscosidade regulados.
Sexta etapa: Cera
Vire os moldes de cerâmica de cabeça para baixo e coloque-os em um forno ou autoclave para derreter e evaporar a cera. Isso faz com que a maior parte das falhas de casca seja causada por resinas com um coeficiente de expansão térmica significativamente maior do que o material de revestimento ao redor delas.
Quando derrete a cera, ela se expande e causa tensão. Aqueça a cera o mais rápido possível para reduzir essas tensões, permitindo que as superfícies externas da cera derretam e drenem rapidamente, permitindo que a maior parte da resina se expanda.
Em alguns casos, faça os furos no molde antes do aquecimento. Você pode coletar e reutilizar a cera que sair do molde.
Etapa sete: pré-aquecimento
Exponha o molde à queima, que aquece o molde a temperaturas que variam de 870°C a 1095°C para eliminar a umidade e os restos de cera e sinterizar o molde.
Depois disso, utilize esse aquecimento para preparar o molde antes de despejar. Enquanto isso, deixe o molde esfriar antes de ser testado.
O pré-aquecimento permite que o metal permaneça líquido por mais tempo, possibilitando um preenchimento mais excelente de todas as características do molde e maior precisão dimensional. Após o resfriamento do molde, é possível corrigir as falhas encontradas com pasta de cerâmica ou cimento específico.
Oitava etapa: Derramamento
O molde de revestimento é então colocado com o lado aberto para cima em um recipiente cheio de areia. O metal pode ser derramado por gravidade ou por meio de pressão de ar positiva ou outras pressões.
Use forças adicionais na fundição a vácuo, fundição inclinada, vazamento assistido por pressão e fundição centrífuga, que são especialmente eficazes quando os moldes têm peças delicadas que, de outra forma, seriam difíceis de preencher.
Nove etapas: Desinvestimento
Martelar a carcaça, jatear, vibrar, jatear com água ou dissolver quimicamente (geralmente com nitrogênio líquido). Remova e recicle o jito. E, em seguida, limpe a fundição para eliminar qualquer vestígio do processo de fundição, geralmente feito por esmerilhamento.
Décima etapa: Acabamento
Submeter a peça fundida acabada ao acabamento após ter sido retificada. Ele elimina as impurezas e os pontos negativos usando ferramentas manuais e soldagem, o que é um passo além da retificação. Se o item precisar de um endireitamento extra, a empresa usa prensas hidráulicas de endireitamento para ajustar o produto às suas tolerâncias.
Aplicação do processo de fundição por cera perdida
A fundição por cera perdida é uma das primeiras tecnologias de fundição e é um monumento ao seu uso que pode ser usado por muitas empresas comerciais e industriais atualmente.
A seguir, apresentamos apenas algumas das aplicações mais populares e essenciais de fundição por cera perdida:
- Em motores e geradores, componentes de engenharia, como rotores e lâminas de turbina
- Componentes da válvula (carcaças, pistões, etc.)
- Fabricação de armas de fogo (gatilhos, martelos, etc.)
- Equipamentos de fabricação do setor de alimentos e bebidas
- Com um uso tão amplo, é razoável concluir que o investimento em ferramentas e equipamentos de fundição tem ajudado praticamente todos os setores.
Fornecedores populares de fundição por cera perdida
Atualmente, a fundição por cera perdida é um bom negócio para oficinas de metalurgia. Há um bom número de fornecedores de fundição de investimento disponíveis nos EUA.
De acordo com a demanda do mercado de 2024, os fornecedores mais famosos de fundição de investimento são Precision Castparts Corp., Alcoa Corporation, Impor Industries USA, Inc., metalTek International, Sigma OEM.
Um resumo rápido sobre fundição por cera perdida versus fundição em areia. Fundição em areia
Às vezes, a fundição por cera perdida é significativamente mais cara do que a fundição em areia devido à complexidade e à preparação necessárias.
A qualidade da superfície do produto final é outra distinção fundamental entre o investimento e a fundição em areia. Seria melhor desmontá-lo para liberar o resultado final de um molde de fundição em areia. Como resultado das linhas de separação no molde, as peças concluídas têm uma costura. A areia um tanto grossa também deixa uma superfície similarmente áspera nas peças fundidas.
A fundição por cera perdida, por outro lado, emprega moldes complexos de cerâmica. As peças acabadas apresentam superfícies lisas, tolerâncias estreitas e paredes finas. As peças fundidas geralmente não precisam de nenhum processamento adicional após a remoção dos gates e sprues.
Como a fundição por cera perdida emprega pasta líquida para produzir os moldes, os componentes fundidos podem ter praticamente qualquer formato, permitindo que os engenheiros incluam detalhes intrincados e geometrias complicadas em seus projetos. Frequentemente, as peças fundidas em areia são afuniladas (com ângulos de inclinação) ou contornadas de forma que possam emergir rápida e suavemente da areia compactada.
A fundição em areia tem a vantagem de ser relativamente fácil alterar o molde para atender às modificações do projeto. Para as versões em cera, os técnicos podem precisar modificar ou substituir o padrão de metal sólido ou criar novos moldes, o que pode ser um procedimento mais complicado com a fundição de investimento.
Vantagens e desvantagens do processo de fundição por cera perdida
A fundição por cera perdida, como qualquer outra tecnologia de produção, não é perfeita. Dependendo da forma de seu modelo, pode não ser uma metodologia apropriada ou pode simplesmente ser muito lenta para o rendimento pretendido. Esses são os benefícios e as desvantagens a serem considerados ao escolher entre a fundição por cera perdida e os métodos alternativos:
Vantagens
Capacidade de reproduzir projetos complexos
A produção de modelos altamente precisos, mesmo aqueles com características minúsculas e paredes finas, é um dos principais motivos pelos quais a fundição por cera perdida é geralmente o processo de fabricação preferido.
O grau de detalhamento do Investment casting é suficiente para empresas que dependem de equipamentos e componentes de alta precisão, como automóveis e aeronaves.
Até mesmo joalheiros com visão de futuro começaram a perceber as vantagens da fundição por cera perdida.
As peças fundidas têm superfícies lisas depois de serem retiradas
Os moldes de metal que saem do molde têm superfícies incrivelmente lisas devido ao fato de o molde ser feito envolvendo o projeto principal com uma pasta de material refratário.
Será necessário algum pós-processamento para que os moldes de metal fiquem precisamente perfeitos, mas isso levará muito menos tempo e esforço.
A precisão dimensional é excelente
Os materiais refratários para o molde na fundição de revestimento ajudam a manter as proporções originais do padrão mestre. Quando submetida ao calor, essa estabilidade dimensional se traduz em peças fundidas de metal que são, em termos de escala, fiéis ao padrão original.
A fundição por cera perdida pode atingir tolerâncias tão baixas quanto 0,076 milímetros, de acordo com especialistas.
Desvantagens
Os ciclos de produção são mais longos
Embora alguns elementos do processo de fundição por cera perdida possam ser automáticos, ele ainda é muito mais lento do que outros processos de produção. A fundição por cera perdida pode representar um dilema para os setores que dependem de um alto volume de produção e de uma rápida rotatividade.
Caro
Embora o processo de fundição por cera perdida pareça simples, ele é um procedimento caro devido ao alto custo dos materiais e dos equipamentos especiais. Nesse caso, há muito trabalho físico envolvido, e você também deve considerar o custo da entrega.
Se você estiver fazendo uma produção em pequena escala, a economia do casting de investimento pode não se sustentar.
Não recomendado para projetos com núcleos
Você pode usar a fundição de revestimento para fazer coisas incríveis, como lâminas de turbina ou carcaças de bombas. No entanto, se o formato do seu modelo tiver um núcleo oco, talvez seja necessário investigar formas alternativas e mais adequadas.
Resumo
O processo de fundição de investimento é um processo de fundição de metal muito popular no mundo. Com base na discussão acima, descrevemos o processo de fundição de investimento passo a passo. Esperamos que seja claro o suficiente para entender cada um dos processos de fundição mencionados.
Entretanto, a fundição por cera perdida é um método excelente e benéfico para a fundição de metais. Mas ele também tem algumas considerações. Nesse caso, ele tem alguns prós e contras. Nós também os descrevemos.
Além disso, também demonstramos a aplicação da fundição por cera perdida, fundição por cera perdida versus fundição em areia e o famoso fornecedor de fundição por cera perdida nos EUA.