Metal casting is a contemporary technique with a long history. Various metal forms come through the metal casting process by pouring molten metal into a mold cavity, where it cools before being retrieved from the mold. However, An Investment Casting Process is one of the popular metal casting processes in the manufacturing industry.
What is Investment Casting?
The investment casting process is sometimes known as lost-wax investment casting. Thousands of years ago, humanity poured molten metal into a disposable ceramic mold, making investment casting one of the earliest industrial methods.
Stainless steel investment castings are everyday investment casting products that have a built-in chromium oxide layer that gives superior anti-corrosive qualities, unlike other materials. Stainless steel castings are helpful for military, medicinal, and industrial applications because of their corrosion resistance.
Investment casting creates exact components with the least amount of waste, energy, and subsequent machining. It may also guarantee the manufacture of highly complex parts. For design engineers, this scenario makes the investment casting technique extremely helpful.
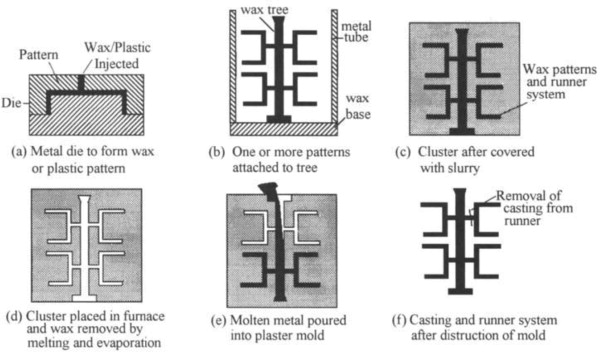
Investment Casting Process
The investment Casting process requires the use of a metal die, wax, ceramic, slurry, furnace, molten metal, and any machines need for sandblasting, cutting, or grinding.
The following is the step-by-step process through which people make various metal forms.
Step One: Pattern Making
A professional mold maker or sculpting artists make a master pattern out of wax, clay, wood, steel, or plastic, depending on the final product specifications.
It considers the shrinkage tolerance for the generated form of wax and casting material the name \”master pattern\” for the two-fold shrinkage allowance. It employs a pattern with identical characteristics as the finished object, except a thermal expansion allowance.
Wax designs are often injection molded onto a metal die and produced as a single piece. In this case, you may use the cores to create any internal pattern features.
Depending on the size, shape, and material used, this method may need some trial and error to get the size and form perfect, making these molds expensive.
A central wax gating system connects multiple designs to produce a tree-like assembly at this stage (sprue, runners, and risers). The gating system creates paths for the molten metal to travel through its approach to the mold cavity.
Step two: Mold Creation
The manufacturing artist makes the master die a mold that suits the master pattern. If the constructed master pattern is of steel, the master die might be cast straight from the design using a lower melting point metal.
You can also cast the rubber molds from the master pattern. Alternatively, you can manufacture a master die without the need for a master pattern.
Step three: Wax Pattern Production
Although wax design usage is common, you can also use other materials such as plastic and frozen mercury. There are two methods of creating Wax patterns.
In one method, You can pour the wax into the mold and swish until an even coating, typically 3 mm (0.12 in) thick, covers the inside surface of the mold. This procedure continues until the required pattern thickness appears.
Another approach includes filling the entire mold with molten wax and allowing it to solidify.
If you require a core, two alternatives are available: soluble wax or ceramic. It intends the soluble wax cores to melt out of the investment coating with the rest of the wax pattern, whereas it removes ceramic bodies once the object has solidified.
Step Four: Wax Patterns Assembly
You can generate multiple wax designs and integrate them into a single colossal design. It casts in a single batch pour. This stage joins the patterns to a wax sprue to form a pattern cluster or tree in this case.
You will need a heating tool to gently melt specific wax surfaces, which are then placed against one other and allowed to cool and firm to join patterns.
Make a tree of up to several hundred motifs. You can also pursue wax designs, which involve rubbing off separating lines or flashings with a hot metal instrument. Finally, dress the patterns to resemble finished items.
Step Five: Application of Investment materials
The ceramic mold, also known as the investment, is made by repeating a series of steps—coating, stuccoing, and hardening until it reaches the necessary thickness.
Coating entails immersing a pattern cluster in a fine refractory material slurry and then draining it to generate a homogeneous surface coating. Delicate materials, often known as prime coats, retain good features from the mold in this first phase.
Stuccoing incorporates coarse ceramic particles into designs by dipping them into a fluidized bed, sanding them using a wet sander, or applying materials by hand. Coatings can be cured after hardening. It continues this process until the investment reaches the desired thickness.
Allow the investment molds to cure fully, which can take anywhere from 16 to 48 hours. Speed up the drying by using a vacuum or reducing ambient humidity. You may also make investment molds by arranging to pattern clusters in a flask and then pouring liquid investment material from above.
IT vibrates the flask to allow trapped air to escape and assist the investment material in filling any tiny spaces.
Silica, zircon, aluminum silicates, and alumina are common refractory materials used to make investments. It often utilizes silica in the form of fused silica. However, Occasionally it uses quartz since it is less costly.
Aluminum silicates combine alumina and silica with an alumina percentage ranging from 42 to 72 percent; at 72 percent alumina, we can call this mullite. It commonly uses zircon-based refractories during the primary coat(s) because zirconium is less likely to react with molten metal.
Before using silica, It utilizes a plaster and crushed-up old molds (chamotte) mixture. Formalized paraphrase Binders used to keep the refractory material in place include ethyl silicate, colloidal silica, sodium silicate, and a hybrid of these that is pH and viscosity-regulated.
Step six: Dewax
Turn the ceramic molds upside down and place them in a furnace or autoclave to melt and evaporate the wax. It causes the bulk of shell failures by resins with a significantly greater thermal expansion coefficient than the investment material around them.
When it melts the wax, it expands and causes tension. Heat the wax as soon as possible to reduce these tensions, allowing the outer wax surfaces to melt and drain fast, allowing most of the resin to expand.
Bore the holes into the mold before heating in some cases. You can collect and reuse any wax that escapes from the mold.
Step Seven: preheating
Expose the mold to burnout, which warms the mold to temperatures ranging from 870°C to 1095°C to eliminate any moisture and leftover wax and sinter the mold.
After that, Utilize this heating to prepare the mold before pouring. In the meantime, Allow the mold to cool before being tested.
Preheating lets the metal remain liquid for a longer time, allowing for more excellent filling of all mold features and increased dimensional accuracy. After the mold has cooled, You can fix any flaws discovered with ceramic slurry or specific cement.
Step Eight: Pouring
The investment mold is then placed open-side up in a sand-filled container. The metal can be poured by gravity or by providing positive air pressure or other pressures.
Use additional forces in vacuum casting, tilt casting, pressure-assisted pouring, and centrifugal casting, which are especially effective when molds have delicate parts that would otherwise be difficult to fill.
Step Nine: Divesting
Hammer the shell, media blasted, vibrated, water jetted, or chemically dissolved (often with liquid nitrogen). Remove and Recycle the sprue. And then clean the casting to eliminate any traces of the casting process, commonly done by grinding.
Step Ten: Finishing
Subject the finished casting to finishing after it has been ground. It eliminates the impurities and negatives using hand-tooling and welding, which is a step beyond grinding. If the item requires extra straightening, it use hydraulic straightening presses to bring the product by its tolerances.
Application of Investment Casting Process
Investment casting is one of the earliest casting technologies, and it\’s a monument to its use that you can use by many commercial and industrial companies today.
The following are only a few of the most popular and essential investment casting applications:
- In motors and generators, engineering components such as rotors and turbine blades
- Valve components (casings, pistons, etc.)
- Manufacturing of firearms (triggers, hammers, etc.)
- Food and beverage industry manufacturing equipment
- With such broad use, it\’s reasonable to conclude that investment in casting-made tools and equipment has helped practically every industry.
Popular Investment Casting Suppliers
Invest casting is a good business nowadays for metalworking workshops. There are a good number of investment casting suppliers available in the USA.
According to the 2024 market demand, the famous investment casting suppliers are Precision Castparts Corp., Alcoa Corporation, Impor Industries USA, Inc., metalTek International, Sigma OEM.
A Quick Summary to Investment Casting Vs. Sand Casting
Investment casting is sometimes significantly more expensive than sand casting due to the intricacy and preparation required.
The surface quality of the end product is another critical distinction between investment and sand casting. It would be best to tear it apart to release the finished result from a sand-casting mold. As a result of the separating lines in the mold, completed pieces have a seam. The somewhat coarse sand also leaves a similarly rough surface on cast pieces.
Investment casting, on the other hand, employs complex ceramic molds. The finished pieces feature smooth surfaces, tight tolerances, and thin walls. The cast pieces usually don\’t need any additional processing after it removes the gates and sprues.
Because investment casting employs liquid slurry to produce the molds, cast components may be practically any shape, allowing engineers to include intricate details and complicated geometries in their designs. It frequently tapers the sand-cast pieces (with draft angles) or contoured such that they may readily and smoothly emerge from the compacted sand.
Sand casting has the advantage of being relatively easy to change the mold to suit design modifications. For wax versions, technicians may need to modify or replace the solid metal pattern or create new molds, which can be a more complicated procedure with investment casting.
Advantages and Disadvantages of the Investment Casting Process
Investment casting, like any other production technology, isn\’t flawless. Depending on the shape of your model, it may not be an appropriate methodology, or it may simply be too slow for your intended throughput. These are the benefits and drawbacks to consider when selecting between investment casting and alternative methods:
Advantages
Able to reproduce complex designs
Producing highly accurate models, even ones with minute features and thin walls, is one of the key reasons why investment casting is generally the favored manufacturing process.
Investment casting\’s degree of detail is sufficient for businesses that rely on high-precision equipment and components, such as autos and aircraft travel.
Even forward-thinking jewelers have begun to see the advantages of investment casting.
Casts have smooth surfaces after they come out
The metal casts that come out of the mold have amazingly smooth surfaces due to making the mold by surrounding the master design with a slurry of refractory material.
It will require some post-processing for the metal casts to be precisely flawless, but it will take considerably less time and effort.
Dimensional accuracy is excellent
Refractory materials for the mold in investment casting help to retain the master pattern\’s original proportions. When subjected to heat, this dimensional stability translates to metal castings that are scale-wise true to the original pattern.
Investment casting may achieve tolerances as low as 0.076 millimeters, according to specialists.
Disadvantages
Production cycles are longer
Even though some elements of the investment casting process may be automatic, it is still much slower than other production processes. Investment casting may provide a dilemma for industries that rely on high production volume and fast turnover.
Expensive
Although the investment casting process appears straightforward, it is a pricey procedure due to the high cost of materials and special equipment. In this case, there is a lot of physical labor involved, you should also consider the cost of delivery.
If you\’re doing small-scale production, investment casting\’s economics might not stand up.
Not recommended for designs with cores
You may use Investment casting to make incredible things like turbine blades or pump casings. If your model\’s shape has a hollow core, however, you may need to investigate alternative, more appropriate ways.
Summary
The investment casting process is a popular Metal casting process in the world. From the above discussion, we have described the investment casting process step by step. We hope it is clear enough to understand each of the casting processes mentioned.
However, Investment casting is a beneficial and excellent method for metal casting. But it has few considerations too. In that case, it has some pros and cons. We have also described them.
In addition, We have also demonstrated the application of Investment casting, Investment casting vs. Sand casting, and the famous investment casting supplier in the USA.