Advanced technology in factories is more critical than ever in making the steel industry more efficient and sustainable. Artificial intelligence is attempting to transform the way “How is steel made.”
“How is steel made?” is a frequently asked topic among our learners. The procedure is straightforward to comprehend. This page will explain the process and show each step of “how is steel made.”
Steel Manufacturing and market Overview
Steel is one of the most widely used metals in today’s world. It’s inexpensive, long-lasting, and versatile. Steel is the world’s second-largest mass-produced commodity, behind cement, with almost 750 million tonnes annual output.
“How is steel made?” is a process that takes place 24 hours a day. Besides, it requires a constant supply of raw materials as well as massive amounts of energy.
According to the World Steel Association, world crude steel production grew from 851 million tonnes in 2001 to 1,606 Mt in 2013. On the other hand, worldwide average steel use per capita increased steadily from 150 kg in 2001 to 225 kg in 2013.
Carbon content in steel ranges from 0.08 to 1.5 per cent. Due to its composition, it’s more challenging to work with than wrought iron. But they are not as brittle as cast iron.
Steel possesses a unique mix of hardness, flexibility, and tensile strength. It is entirely recyclable and uses very little energy. Thanks to the steel industry’s efforts, energy consumption, and CO2 emissions are now less than half of those in the 1960s. As a result of this technique, steel becomes more environmentally friendly and long-lasting.
Steel-based items include rail lines, oil and gas pipelines, towers, elevators, subways, bridges, automobiles, ships, knives and forks, razors, and surgical equipment, to name a few.
How is steel made
“How is steel made” process heat Iron ore is and melt it in furnaces to eliminate impurities and add carbon to manufacture steel. The process produces the majority of steel in one of two ways: a blast furnace or an electric arc furnace.
Blast furnaces employ raw materials, with some scrap steel thrown in for good measure, while Electric Arc Furnaces primarily use scrap steel.
What Is A Blast Furnace?
In the mid-1850s, Henry Bessemer developed the blast furnace. Bessemer came up with a means to make steel by pushing air through molten iron to oxidize it and remove impurities in steel production.
The contemporary blast furnace is a massive steel cylinder lined with heat-resistant brick fashioned like a cylinder. From the top, iron ore, coke, and limestone are fed into the furnace. And then it gradually drops to the bottom, becoming hotter as they do so.
Gas from the burning coke releases oxygen from the iron ore in the upper section of the furnace. Limestone interacts with impurities in the ore and coke to generate slag in the bottom part of the furnace.
Temperatures at the furnace’s bottom reach above 3000 degrees Fahrenheit. A slag notch in the furnace may drain the molten slag. This slag floats on the molten steel. The process then discharges the molten steel from the furnace’s hearth through a tap hole.
What Is An Electric Arc Furnaces?
EAFs are primarily used to create high-quality steel alloyed with other metals in steel production. Ordinary EAFs may also make non-alloyed steels. Unlike furnaces, this process does not employ hot metal. They make use of scrap steel from recyclable materials.
An overhead crane tipped the scrap steel into the EAF. When the furnace is full, the machine shuts the lid covering the top of the furnace. And then it drops the electrodes into the furnace via the lid. The process applies a strong electric current to the electrodes. It creates heat and melts the scrap.
Steel production adds Ferro-alloys to the steel while it melts to give it the proper chemical composition. After that, the machine pumps oxygen into the furnace to cleanse the steel. Lime and fluorspar are added to the impurities, causing them to fuse and generate slag.
The molten slag floats on top of the molten steel by tilting the furnace and may be drained off. By mixing various metals to generate steel alloys, EAFs can produce a variety of high-quality steels. Stainless steel, chromium, and nickel are the most extensively used corrosion-resistant qualities.
Steels utilized in engineering, aerospace, and armour plating are among the other specific steels produced in EAFs.
How is steel made in a steel factory
Steel factory makes steel from either iron ore or scrap metal. Iron ore is a mineral aggregate that can be processed economically into metal iron.
The composition of the iron ore determines its grade. A high iron concentration with low sulphur and phosphorus levels is desirable. The world is full of iron ore; however, its iron concentration varies depending on the location and ecological factors.
“How is steel made” first collects the steel scrap and repurposes them as a valuable raw material for steel manufacturing for many decades.
Please keep in mind that BF primarily employs raw materials, with some scrap steel thrown in for good measure, while EAF mainly uses scrap steel.
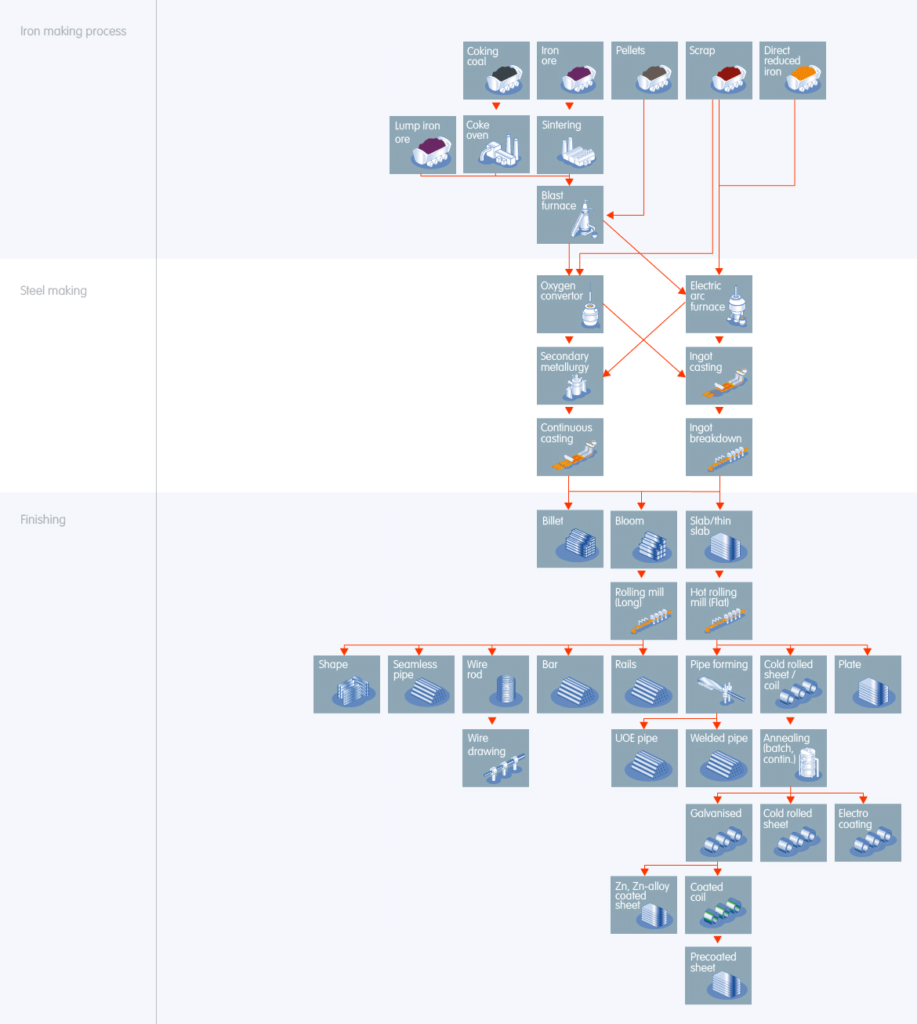
Iron Making Process
“How is steel made” requires molten iron to produce steel. Iron ore and coal are the two primary materials used to make molten iron. Steel factory turns the iron ore into sinter ore in a sintering plant and converts coal to raw coke in a coke oven.
Steel production then dumps the processed materials into a blast furnace. It heats it to 1200°C by hot air forced in by tuyeres from the bottom. It produces molten iron by oxidizing the coke and reducing the sintered ore. Take a look at the diagram above.
Coke oven preparation
Multiple ovens comprise a coke battery in steel production. Before “How is steel made” charges it in a coke furnace, it crushes and mixes the coal. After that, the steel production delivers the mixed coal by a larry vehicle to each oven.
The process heats the coal to 1,800°F in the coke oven for up to 18 hours. It pushes the coal into the off-gas during this period, leaving a pure carbon form known as “coke.”
When the steel production exposes coke to oxygen, it instantly ignites and burns. When the process pushes coke out of the furnace and into a railcar, it quenches the coke to cool down and halt the burning process.
After cooling, “how is steel made” deposits the coke into a coal dock. After that, it transports it to a filter and sized facility before putting it into the blast furnace.
Sintering
Sintering is a thermal agglomeration technique for iron ore fines in the steel production process. This process recovers ironmaking products, fluxes, slag-forming agents, and solid fuels.
The goal of the sintering process is to create a product with suitable properties to feed into the blast furnace.
The process has been extensively investigated to determine the ideal conditions for obtaining the most excellent sinter quality. The sintering process highlights that the mixture undergoes once granulated and fed onto the sinter strand.
At a temperature of 1300-1480°C, “how is steel made” melts the sinter mixture. It creates the sinter cake through a series of processes. And then it put into the blast furnace to make pig iron.
Blast Furnace
Steel production first and foremost requires iron and carbon. Iron is not very strong on its own, but a low carbon content – less than 1%, depending on the kind of steel – provides it with crucial qualities.
Steel gets its carbon from coal and its iron from iron ore. On the other hand, iron ore combines iron, oxygen, and other trace components. Steel is created by separating iron from oxygen and adding a small quantity of carbon.
However, the process melts both at a high temperature in the presence of oxygen and coal called coke.
The iron ore releases oxygen at high temperatures, transported away by the carbon from the coke in carbon dioxide.
Fe_2 O_3(s) + 3 CO(g) → 2 Fe(s) + 3 CO_2(g)
The reaction happens because carbon dioxide has a lower energy state than iron oxide. Besides, the process requires high temperatures to reach activation energy. It has an excessively high carbon content. Besides, a small amount of carbon combines with iron is an intermediate before steel.
Steel Making
A torpedo vehicle transports the molten iron to the steel factory, pumps it into a converter. And then the “How steel is made” blasts the converter with oxygen, burning all impurities away. Pure molten steel is all that remains.
Continuous casting
“How steel is made” process pours the molten metal into a casting machine. This continuous casting process make billets, blooms, or slabs. It reduces the need for primary and intermediate rolling mills, soaking pits, and vast quantities of ingot moulds to store and utilize.
It also improves the yield of useable products from a given steel weight. The process is done by processing them into a semi-finished shape closer to the completed product.
An overhead crane transports a ladle of steel to the continuous casting facility. After pre-treatment, which may include stirring with an inert gas. However, the open mouth of the ladle is covered by an insulating lid to limit heat loss.
The steel production raises the whole device onto a revolving turret via crane. Sequence casting is now conceivable of the same grade steel without halting the machine. It is also a significant cost-cutting component.
However, the steel production process connects a gas-tight tube to the exterior of the ladle nozzle before the casting process. This mechanism prevents liquid steel from absorbing too much oxygen and nitrogen from the air.
After that, the “How is steel made” process opens the ladle nozzle. And then it enables the steel to flow at a regulated pace from the spoon into the tundish. After that, a reservoir supplies the water-cooled copper mould of the casting process.
The steel is dragged downwards from the bottom of the mould via a curving network of support rollers. After that, it sprays water until it emerges horizontally as a solid steel slab from the machine’s discharge end.
Ingot breakdown
The “How is steel made” process depends on steel ingot soaking direct rolling technology, which includes the following steps:
- The process applies a steel ingot thermal condition model as a theoretical foundation.
- When water is sprayed into the top and bottom of a steel ingot simultaneously, it reduces the time it takes to complete pouring the steel ingot. And then it finishes furnace loading.
- The production process carries out furnace loading and dense furnace loading according to groups. It creates a closed-type flue shutter, a close air and gas valve, and a close air and gas flue shutter. Finally, the process rolls the steel ingot after a soaking period has passed.
Finishing
The practice of altering the surface of an item to enhance its aesthetic and longevity is known as metal finishing. Electroplating forms a thin surface coating of metal on another through electrodeposition.
Primary Forging
The finishing stage moulds the roughcast pieces into forms by hot rolling in this phase. It eliminates form flaws and produces the required steel grade. This method may create seamless tubing, long and flat goods, and various custom things.
Secondary Forming
Coating, heat treatment, joining, pressing, drilling, machining, and riveting are secondary processes that give the steel its final form.
Conclusion
Above all, we have discussed the overall “How is steel made” process. This article would be helpful if you’re working on a steel project. You may also need some expert advice on what method to use or what sort of steel to utilize.
Leave a Reply
You must be logged in to post a comment.