Proper Maintenance increases a machine’s lifetime. As a result, cleaning the equipment is essential for productivity and service life. Dry ice blasting is a standard industrial cleaning method used in various industries.
Dry ice cleaning is the most excellent method to clean any machine or equipment, and although it is a little pricey, it is also ecologically beneficial.
On the other hand, this article will introduce you to the dry ice cleaning method. In addition, we’ll take a quick look at this cleaning method application.
What is dry ice blasting
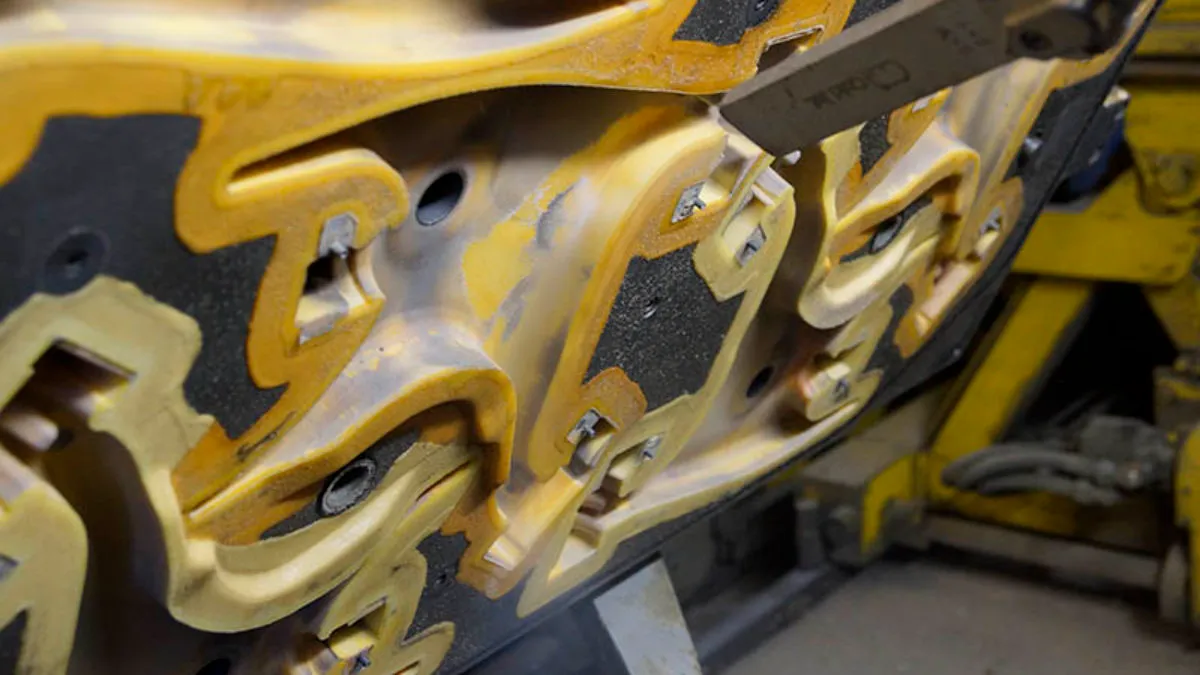
Dry ice blasting is a kind of non-abrasive blasting in which dry ice (the solid form of carbon dioxide) is accelerated and directed at a surface to clean it. This process is a strong, mild, dry, and environmentally friendly cleaning procedure in several sectors.
Dry ice cleaning is comparable to sandblasting, plastic bead blasting, or soda blasting, except that the blasting media is dry ice instead of water. Because dry ice sublimates at ambient temperature, dry ice blasting leaves no chemical trace.
Dry ice cleaning, CO2 blasting, and dry ice dusting describe dry ice blasting. The dry ice cleaning machine is a cost-effective technology that minimizes or eliminates staff contact with chemical cleaners.
However, the EPA (Environmental Protection Agency), FDA (Food And Drug Administration), and USDA (United States Department of Agriculture) have all allowed the use of dry ice cleaning machines.
How does dry ice Cleaning works
Dry ice cleaning entails rapidly pushing pellets. Dry ice pellets are less thick and soft than conventional blast-cleaning mediums.
However, the pellet sublimates virtually instantly upon contact, transmitting very little kinetic energy to the surface and causing minimal abrasion. Thermal shock causes shear strains as the sublimation process takes substantial heat from the surface.
The process predicts transmitting more heat to the top layer of dirt or contamination than the underlying substrate and peeling off more readily. Hence, we intend this method to enhance cleaning.
In particular, the heat conductivity of the substrate and contaminant affects the efficiency and efficacy of this procedure. The quick transition from solid to gas generates minuscule shock waves that are supposed to aid in the removal of the pollutant.
Dry Ice Blasting is safe
Dry ice cleaning is a flexible and surface preparation procedure used on practically any surface. In particular, it can remove grease, oil, filth, dust, adhesives, paints, food residue, germs, tar, soot, greasy smoke residue, mould, ink, paper dust, resin, and more.
Particularly, Dry ice cleaning is a popular cleaning procedure in most industrial settings. The dry ice blasting process is entirely safe for human beings.
Non-Abbrasavie and Dustless
Even though shooting dry ice pellets seems severe, it is non-abrasive according to the physics of thermal shock. The process removes the coating or contaminant without a trace or a scratch due to the substrate’s contraction and the gas’s expansion as it sublimates.
On the other hand, Dry ice cleaning machine produces no dust. As the popularity of abrasive blasting has grown, removing pollutants from the air has become a desired feature.
Cleaning leaves no residue
Dry ice sublimates quickly and leaves no trace on the surface. In this case, the media dissolves into the air, minimizing the amount of time it takes to clean up.
Consecutively, the machine removes, sweep, or vacuums away the coatings and impurities. As a consequence, cleanliness and efficiency have increased.
Accurate in cleaning
A dry Ice cleaning machine is a perfectly safe procedure for any cleaning application.
Cleaning using dry ice pellets provides more precise and focused cleaning. The compressed dry ice may also penetrate a crack to reach hard-to-reach areas between wood planks. It may penetrate where the wire is kept and be safe on electrical wiring.
Non-toxic
Cleaning with dry ice is a non-toxic method. Because it depends on the subzero temperature to remove coatings, kill germs, and destroy fungi on the surface, it does not employ chemicals or solvents.
The Food Standards Agency has approved dry ice cleaning for food processors. When conducted in open locations, it poses no dangers or hazards to the operators.
Non-conductive process
Cleaning with dry ice is a non-conductive method. As a result, it is not harmful to electrical components. It removes the need to disassemble machines, reducing downtime and allowing you to return to operation fast. However, If you follow the correct safety precautions, you may clean most equipment without being completely stopped down.
Dry ice cleaning compare to other cleaning methods
Dry ice blasting, sandblasting, soda blasting, wet ice blasting, and laser cleaning are all standard cleaning methods. They do, however, have certain similarities and differences.
Let’s compare and contrast the various blasting methods with dry ice cleaning.
Dry Ice blasting vs sandblasting
When opposed to sandblasting, dry ice blasting has some advantages, one of which is non-abrasive. Sandblasting is an abrasive way of eliminating contaminants that might harm the surface.
On the other hand, for electrical applications, sandblasting is not the best option. Both dry ice and sandblasting are not electrically conductive.
The use of dry ice cleaning to remove unpleasant compounds from surfaces is a non-toxic option. Sandblasting may create a toxic hazard waste to remove dangerous chemicals or materials.
Because the dry ice sublimates upon contact, there is no additional waste from dry ice blasting. When you employ sandblasting, it generates a lot of secondary trash, which may cause delays and increase costs.
The most ecologically friendly blasting method is dry ice cleaning. Although sandblasting is biodegradable, it may also be damaging to the environment.
Dry Ice Blasting | Sand Blasting |
Non-Abrasive | Abrasive |
No Secondary Wastes | Generates Secondary Wastes |
Environmentally Responsible | Not Environmentally Responsible |
Dry Ice blasting vs soda & wet ice blasting
The creation of soda blasting and dry ice blasting technologies were in response to the same problem. Different sectors use both for applications requiring a gentle touch on the substrate, such as cleaning and coating removal.
Wet ice blasting is a unique form of media blasting method that requires proprietary technology to harness the strength of ordinary ice cubes.
Operators may use a little more abrasive blast cleaning technique with this kind of ice blasting than they can with dry ice cleaning.
One of the essential benefits of wet ice (ice cube) blasting is the cost savings on media. Wet ice media is much less costly than dry ice and commercial grade sodium bicarbonate.
Dry Ice Blasting | Soda & Wet Ice Blasting |
Expensive | Comparatively Cheap |
No Abrasive | Abrasive |
Dry Ice blasting vs laser cleaning
Laser cleaning has some limitations to a small number of cleaning applications. In this case, the technology used by ice blasting machines and laser cleaning equipment is very different.
Laser cleaning is an entirely distinct debris removal process that does not need ice particles. The dry ice cleaning machine uses compressed air, but the laser cleaning machine doesn’t.
Dry ice cleaning, wet ice blasting, and laser-blasting have different prices. Laser cleaning is only appropriate for a small number of cleaning tasks.
Dry Ice Blasting | Laser Cleaning |
Uses Compressed Air | Uses Laser Light |
Non-Abrasive | Non-Abrasive |
Expensive | Comparatively Cheap |
Applications
Dry Ice Blasting is a non-abrasive, non-toxic, fully dry industrial cleaning technology with no blast material cleanup. The following list the 15 most popular dry ice cleaning applications.
Adhesive Removal
Adhesive removal using dry ice cleaning is a faster and more effective method of eliminating sticky accumulation on industrial equipment. Dry ice’s low temperature weakens the binding between the adhesive and the surface, allowing easier removal.
Dry ice blasting is non-abrasive and produces no secondary waste, allowing for more frequent cleaning and longer equipment life.
Asphalt & Bitumen Removal
Allowing asphalt materials to pile up on equipment causes quality issues and reduces component lifetime.
Traditional means of cleaning asphalt, bitumen, and tar off paving equipment, trucks, or tanks, such as pressure washers, chemicals, or chisels, may be time-consuming and damaging to the environment.
Cleaning with dry ice blasting is a safer and quicker option since it is fully dry, non-toxic, and produces no secondary waste. Keep your equipment in top functioning order while boosting environmental measures even while operating in low conditions.
Automation Restoration
Automotive repair also requires smart tools that provide the user with total control and adaptability to clean the entire range of auto components.
However, Dry ice cleaning is a non-abrasive, non-corrosive cleaning method that generates no secondary waste.
The dry ice cleaning machine fine-tunes cleaning aggressiveness to clean any car component efficiently. It also prevents the possibility of delicate parts.
Coatings & Corrosion Removal
Projects will see a reduction in containment and post-clean-up expenses due to the significant reduction in dust and trash.
Because dry ice blasting does not need rust inhibitors or induce flash rusting, the surface will be left dry and residue-free, allowing for a faster application of a new coating.
Coffee Roaster Cleaning
Burnt-on coffee grounds clog up coffee roasters, grinders, and packaging machinery.
Manually scrubbing coffee roasters using hand tools is time-consuming and labor-intensive. One roaster takes around eight to ten hours to clean by hand. This process may also entail the addition of water, which might contribute to bacterial growth and a more extended drying period.
Dry ice cleaning systems for coffee roasters and packing equipment are faster and do not produce any secondary waste or need water. A dry ice blasting machine can clean a roaster in less than two hours.
It also safely cleans food-grade surfaces, does not add foreign material or allergens, and reduces the risk for microbial growth and cross-contamination.
Composite Tool Cleaning
By removing the need for harsh chemicals, wire brushes, and abrasive pads, dry ice blasting improves the life of composite moulds and equipment.
The method is non-abrasive and preserves the mould surface polish while protecting the essential dimensions and geometric features of separating lines and sealing surfaces.
Core Box cleaning
Resin and sand accumulation on core box vents inhibits core material from solidifying and often causes vent blockage, lowering product quality and resulting in waste. Traditional cleaning procedures are time-consuming, ineffective, and destructive to tools and core boxes’ vents.
Dry ice blasting eliminates the accumulation fast and safely while the core boxes are still operational, resulting in no additional waste.
It’s a non-abrasive procedure that won’t harm screens, vents, or equipment. Dry ice cleaning of core boxes results in a considerable decrease in production downtime and scrap rates.
General Equipment Cleaning
Dry ice blasting cleans all sorts of production and auxiliary equipment without causing damage to surfaces, generating secondary waste, or endangering personnel or the environment.
Historical Restoration
Dry ice cleaning for historical restoration particularly provides for the safe and successful repair of historical artefacts in a fraction of the time required by other procedures.
However, the procedure is non-abrasive and won’t harm sensitive cleaning surfaces. Dry ice blasting removes the need for abrasive hand tools, hazardous chemicals, and water in manual cleaning.
Finally, Dry ice cleaning removes layers of paint, carbon, pollution, smoke damage, mold, and various other impurities from a variety of surfaces.
Mould Cleaning
Dry ice blasting is non-abrasive, produces no secondary waste, and enables you to clean your moulds while the press is running. It results in increased production, better-quality components, and lower prices.
Using this method, you may clean any mould and a range of moulds finished, including A1 surfaces and textured surfaces.
Nonwoven Die Cleaning
Manufacturers of polymer nonwoven materials use dry ice cleaning machines to increase production speeds. Cleaning is essential for maintaining and enhancing product quality and production, regardless of whether the product is spunbond, melt-blown, wet-laid, or needle-punched.
Using traditional techniques, cleaning a melt-blown die might take several hours and numerous shifts. Depending on the size of the die, cleaning with dry ice blasting MicroParticles takes just minutes. It cuts down on production downtime dramatically.
Parts Finishing
Components finishing dry ice blasting eliminate burrs and flash from machined and molded parts.
In this case, Dry ice is non-abrasive and produces no secondary waste, ensuring that it preserves the completed part’s geometries without the need for residual media.
Remediation
The technique eliminates manual cleaning and produces no secondary waste, saving time on encapsulation and garbage collection and disposal.
Dry ice cleaning helps clean hard-to-reach locations such as tight truss angles around nails, wiring, and plumbing without causing damage to the surface integrity. The technique also minimizes or removes odors caused by fire, smoke, and mold damage.
Surface Preparation
Dry ice cleaning also removes the requirement for surface pretreatment with aqueous or chemical solutions. In this case, the procedure is suitable to remove pollutants from fragile plastic surfaces and significant contaminant accumulation on metal and steel surfaces for a quick repair or non-destructive testing.
Dry ice cleaning leaves no residue on surfaces and prevents grit entrapment, resulting in higher-quality products and more precise testing measures.
Weld Line Cleaning
Above all, By successfully eliminating weld slag, spatter, resin, smoke, oil, and damping adhesive buildup from robots, manufacturing equipment, and auxiliary equipment, dry ice cleaning minimizes misalignment, failures, and scrap.
It was a great thing to know that dry ice blasting is the quickest way to get rid of adhesive material. I need to change my modular system in the kitchen, and I don’t know the best way to do it. It’s very fortunate that I came across your article, I’ll make sure to avail for the best dry ice blasting services in the market.