Anodizing aluminum is one of the most frequently used materials in the production of tools and equipment. You may find anodized components in various places, including home items, construction equipment, and showpieces. Specially anodized aluminum is widely popular in the construction tools and equipment sectors.
What exactly is anodized aluminum, though? That’s what this article is going to demonstrate. It will go through an overview of anodizing aluminum, including varieties, production processes, and applications. Furthermore, it will go through the characteristics and thickness of various kinds.
What is Anodizing?
Anodizing is, in a nutshell, an electrolytic process. It generates an electrolysis process, which involves anodic oxidation and cathodic reduction, using an electrical current. An alumina layer nearly completely coats the aluminum anode at this stage.
The thickness of the surface oxide layer thickens during anodic oxidation. You may alter its structure and properties in response to changes in the electrolyte’s nature, composition, temperature, treatment duration, and voltage.
The component will be more or less robust depending on the thickness of the anodized coating. When the components must be robust, You may raise the thickness to 50 m instead of the typical 5-10 m for ornamental items.
Anodizing Aluminum
Aluminum has been treated to provide a very durable coating is the aluminum anodizing. An electrochemical technique in which the study submerges the metal in a succession of tanks produces anodized aluminum. It forms the anodic layer directly from the metal.
This anodized metal will never crack, flake, or peel since the process makes it from aluminum rather than spray-on. It is much more durable than any other comparable product on the market. Anodized aluminum is three times tougher than raw aluminum and 60% lighter than similar metals such as stainless steel and copper.
How to Anodize Aluminum
The process anodizes aluminum extrusions to prevent corrosion, enhance lubrication, and allow for color dyeing via an electrochemical conversion process. It doesn’t paint or plate this aluminum oxide on the surface; instead, the method merges it entirely with the underlying aluminum substrate so that it won’t chip or peel.
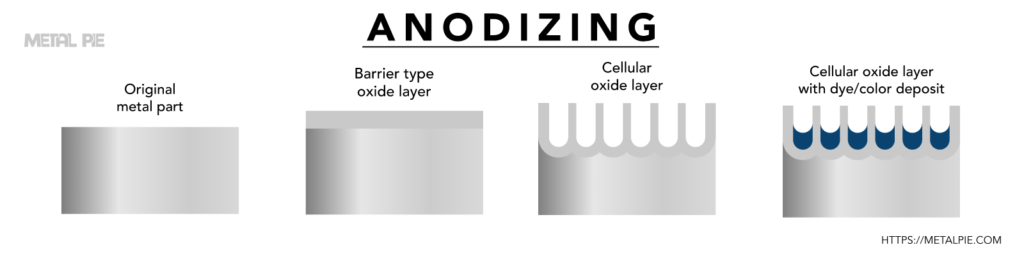
Pre-treatment
Pre-treating the aluminum with degreasing and pickling and giving a visible finish is the first stage in anodizing. To achieve the desired appearance, you may use bright or satin finishes. This step uses light etching in satin finishing to produce an even, matte surface on the metal. Cleaning any heavy metal deposit from the aluminum that the process didn’t eliminate during the pre-treatment procedures is bright finishing. Aluminum extrusions with a bright or satin finish offer a smooth, clean surface for anodizing.
Anodic oxide
This step requires submersion of the material in an acid electrolyte solution while an electric current flows through for anodizing. It changes the metal to the amount needed during this procedure, which is controlled oxidization. You may add the colors to aluminum after anodizing it in a variety of ways.
Colour anodizing
You may do this color anodizing aluminum in a variety of ways. Electrolytic coloring, which includes soaking anodized aluminum in an inorganic metal salt solution, is one method. As the metal salts oxidize in the aluminum pores, the process supplies an electric current to the solution.
The color of aluminum will change depending on the chemical conditions of the bath and the amount of time spent submerged. Gold, black, stainless, transparent, brown, bronze, and nickel are popular anodized color treatments. Color matching and bespoke color anodizing are also available from specific businesses that use sophisticated technologies.
Sealing
This step seals the aluminum at the end of the anodizing process to prevent corrosion and water leakage. You may use a cold technique, a hot procedure, or a mix of the two to seal the anodized aluminum extrusions. This step also protects the surface from being scratched or stained.
Types of Anodizing
According to the Mil-A-8625 classification, there are three kinds of anodizing: Type I-Chromic Acid Anodize, Type II-Sulfuric Acid Anodize, and Type III Hard Anodize or Hardcoat. Phosphoric acid and titanium anodize are two less frequent kinds. Anodizing is a porous structure that develops from the primary aluminum and readily absorbs the colorful dye.
Chromic Acid Anodizing (CAA)
Chromic acid anodizing, also known as type I anodizing, produces the thinnest anodic coat of the three main kinds, measuring between 20 to 100 micro inches per surface. Despite its thinness, chromic anodize provides comparable corrosion protection to aluminum as thicker sulfuric and hard coat anodize when adequately sealed.
Chromic anodize has a grayer appearance and absorbs less color when dyed since it is thinner. As a result, the process limits the use of chromic acid anodizes as a decorative treatment. However, You may color It black as a non-reflective, protective coating on optical component housings. Even black dyed chromic anodize has a softer (grayer) look than sulfuric black anodize.
Boric-Sulfuric Acid Anodizing (BSAA)
Due to environmental, worker safety, health issues, and the expenses involved with utilizing hexavalent chromium-bearing procedures like CAA, Boric-Sulfuric Acid Anodize (BSAA) is an alternative to chromic acid Anodizing.
Aircraft and aerospace components are among the most common uses. MIL-A-8625, Type Ic, and aerospace standards. It’s used to keep paint from peeling and rusting. Paint adhesion is on par with or better than chromic acid, and the method uses less energy than chrome-based procedures.
Sulfuric Acid Anodize (SAA)
The most frequent technique for anodizing is using sulfuric acid. The sulfuric acid anodize method produces films that are between 0.0001″ and.00001″ thick. The coating’s total thickness is 67 percent penetration in the substrate and a 33 percent increase over the part’s initial dimension. It’s ideal for applications that need a high level of hardness and abrasion resistance.
However, the corrosive acid residue is undesirable when it exposes the components to significant stress. The porous nature of sulfuric acid coatings before sealing makes colorful surface finishes on aluminum and related alloys possible.
Hard-Anodized (Hardcoat
Hardcoat anodizing is thicker and denser than sulfuric anodizing, typically done with a sulfuric acid electrolyte. The process uses Hardcoat on aluminum components subjected to high wear or corrosive conditions and needs a thicker, more rigid, longer-lasting coating.
It’s also useful if you need more electrical insulation. Because the method may produce hard coats up to several thousandths of a millimeter in certain instances, anodizing is viable for resurrecting old or mismatched components.
Benefits of Anodizing aluminum
Anodized aluminum has been available for over a century, with some of the first recorded applications dating back to the early 1920s, when it was employed to protect seaplanes against seawater corrosion. People have utilized it in a variety of different applications since then. Anodized aluminum, on the other hand, has many significant advantages over regular aluminum.
Durability
Anodizing Metal is a rigid material, to begin with, but the anodized surface becomes even more rigid than the primary aluminum after the process. Anodized metal has a three-fold more rigid surface than regular aluminum and will not crack, flake, or peel, even when colored.
Appearance
Anodized aluminum has a beautiful finish that adds to the attractiveness of any object. Anodized aluminum is a brilliant new silver hue when left natural, and it may be anodized to give a matte or bright surface. To give it a distinct appearance and feel, you may also add a custom texture to your product, such as stucco, brushed, or pebble tone.
Color Stability
Exterior anodic coatings are resistant to UV radiation, do not crack or peel, and are simple to apply.
Custom Color Option
You may polish the anodized metal to match almost any brand color or Pantone swatch you can envision because of the open pore structure of the anodic layer before sealing. Because of the material’s flexibility, you can create it to resemble various metals, giving you the look of gold, bronze, copper, stainless steel, brass, and more without the danger of rusting.
Lightweight
Anodized aluminum is a lighter metal than stainless steel, copper, or brass, weighing around 60% less.
Increased Adhesion
Anodized aluminum has a higher adherence to adhesives and primers than unanodized aluminum. This situation is due to the deeper holes in the oxide surface of anodized aluminum than ordinary aluminum. When adhesive, primers, or liquids are applied to the surface, the pores act as holes through which the adhesive, primers, or liquids will flow. Greater stickiness is possible because the anodized metal absorbs the fluids.
Corrosion Resistance
Anodized aluminum has a higher corrosion resistance than regular aluminum. Aluminum, whether normal or anodized, cannot rust. They may nevertheless corrode when exposed to moisture, air, salt, or other corrosion-inhibiting chemicals or elements.
Cost
Reduced initial finishing costs coupled with lower ongoing maintenance expenses to provide better long-term value.
Health and Safety
Anodizing is a harmless procedure that has no negative effects on human health. Anodized finishes are chemically stable, do not degrade, are non-toxic, and can withstand temperatures up to the melting point of aluminum.
Anodized Aluminum Application
You may utilize anodized aluminum in any application where another metal is already present. We have illustrated the following common industries where anodized aluminum is widely popular.
- Architecture: Anodized aluminum never rusts, patinas, or weathers, making it a popular option for contemporary building exteriors and interiors. Anodized aluminum is an appealing, lightweight, and inexpensive choice for interior finishes, including ceiling panels, shop signs, and elevator panels, because it can be produced to order in any color, gloss, or texture.
- Transportation: Anodized aluminum is three times harder than the raw material and operates at any speed. Anodized aluminum provides the durability and weather resistance vehicles need. The outstanding beauty customers want in everything from commercial airplane interiors to rail car panels to the brilliant exterior trim on sports cars.
- Consumer Goods: Customers desire goods that are appealing, long-lasting, and represent their aesthetics and lifestyle. Anodized metal can provide you with any appearance, texture, or color you want. Anodized aluminum offers the flexibility and quality your customers expect, from kitchen backsplash panels to microwaves, coffee machines, and other consumer products.
Conclusion
Anodized aluminum may be a stunning element of any project or product, whether you’re constructing magnificent skyscrapers and structures, artwork, the newest range of luxury cars, or high-end appliances. The anodizing technique is environmentally benign and results in an unrivaled finish in dynamic beauty, endurance, and durability.
We hope this article has contained a general idea on what is anodizing aluminum and how to anodize aluminum. Stay with Metalpie for more interesting topic that you didn’t know.
Leave a Reply
You must be logged in to post a comment.