Steel pipes are remarkable materials used in many industries. Because of their excellent strength and ability to withstand high loads, steel pipes are so famous. They also take part in transporting fluids, gases, and other materials. In construction & infrastructure, steel pipes also play a crucial role. So, we can see that steel pipes are necessary in every industry. Therefore, the development of steel pipe fabrication is crucial as well.
This article aims to discuss the fundamentals of the steel pipe fabrication process. It especially highlights the four types of SS pipe fabrication methods. We will learn these methods used for different types of steel pipes. Let’s explore more.
What is Steel Pipe Fabrication?
Simply, we can say that the manufacturing process of steel pipe is called steel pipe fabrication. It actually transforms raw steel materials into custom-designed tubes. Each fabrication process is meant to meet specific requirements for various applications. The steel tube fabrication process may vary based on different steel pipe types. Yes, this is the main content of our today’s article. In the later section, we will talk about more about these processes.
Steel pipe fabrication processes play a crucial role in providing customized solutions. By understanding the specific demands of each application, these fabrication methods may vary. They may need to modify the pipes’ size, thickness, and configuration to meet precise applications.
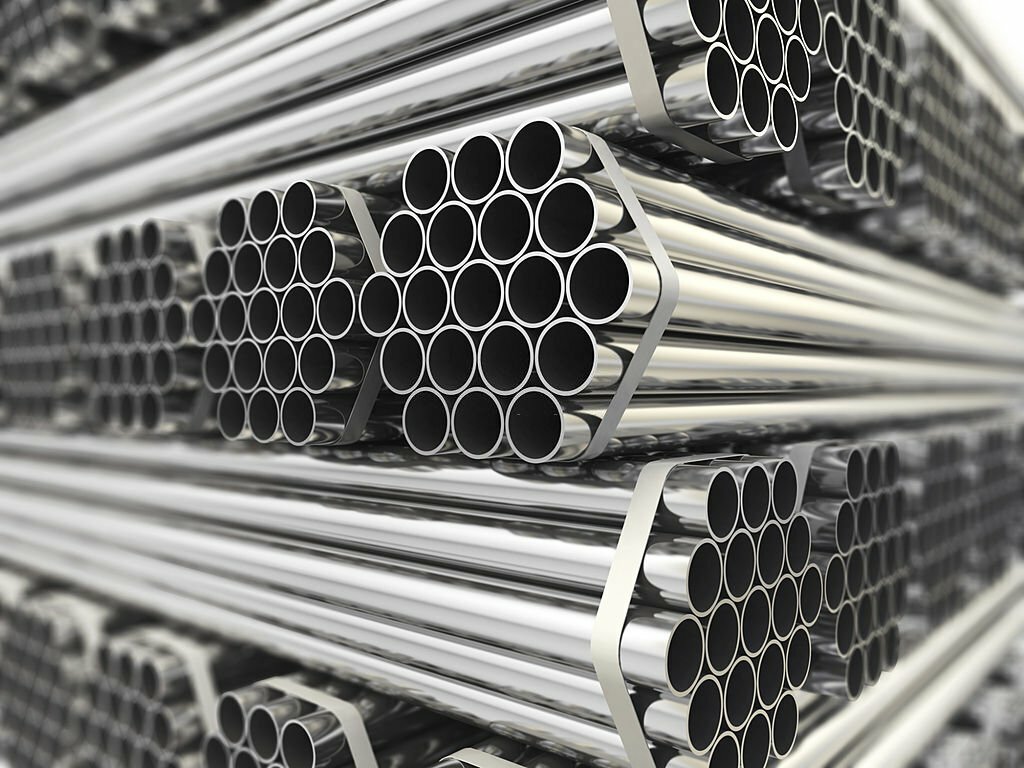
Types of steel pipe
Based on different manufacturing processes, steel pipes are categorized into two main types. These varieties arise from variations in fabrication methods. It impacts the pipe’s structure & characteristics. Understanding these manufacturing processes is crucial. Why?? Because it is essential for selecting the most suitable tubes to meet specific demands.
We can look at the surface of the pipe while comprehending these two types. A straight, thick line on the tube indicates it has been welded. The pipe is seamless if there are no lines or continuous difficulties on the surface. Let’s check out some academic indications.
- Seamless stainless steel pipe: It’s a single piece of steel without any welded joints. The four primary methods of manufacturing seamless steel pipe ensure a uniform structure. They also provide exceptional strengths. Indeed, a seamless steel tube is superior to stainless steel welded pipe. The benefit of seamless reduces the risk of leaks. In addition, it enhances the pipe’s ability to withstand high pressure & temperature conditions.
- Stainless steel welded tubes are made by joining the steel or coils through welding. The benefit of these steel pipes is the ability to produce pipes with diverse diameters & thicknesses. They are cost-effective solutions for many industries. They also have four primary production techniques, like the seamless pipe fabrication process.
Seamless Steel Pipe Fabrication Process
The outstanding features of seamless steel tubes have made them very popular across a wide range of sectors. Examples include the oil & gas industries. In these industries, seamless steel pipe is often used to convey corrosive fluids. On the other hand, seamless stainless steel pipe is often used in high-temperature applications too. They ensure durability & dependability in the power generation and nuclear industries.
Based on pipe dimensions & budget, manufacturers employ four major seamless pipe fabrication methods. All four fabrication processes discussed below begin with similar procedures. The following are the initial formalities:
- Billet Preparation: The processes begin with the selection of a high-quality steel billet. It is actually a solid round or cylindrical metal bar.
- Heating: The chosen billet then undergoes an appropriate heating process. This step enhances its plasticity and makes it easier to deform & shape.
They then apply some similar finishing touches following distinct manufacturing phases. They are as follows:
- Cooling & Cutting: This stage cools the heated pipes and then cuts them into specified lengths.
- Straightening: The cut tubes undergo straightening to ensure uniformity.
- End Facing: Finally, the process ends the production by facing the ends of the steel tubes. This stage is necessary to achieve smooth & even surfaces.
Mandrel Mill Process
The Mandrel Mill technique is named after the mandrel, which is an important tool in the production process. During the piercing step of the procedure, a mandrel is a rod or shaft placed into the hollow tube or pipe. Mandrels, on the other hand, help in piercing, dimensional accuracy, and surface quality. The stages of the process are as follows.
- Piercing: This is the most important part of the mandrel mill process. A mandrel pierces those heated billet and creates a hollow tube.
- Mandrel Milling: The pierced tube then undergoes mandrel milling for dimensional accuracy. It also provides appropriate internal surface quality.
- Stretch Reducing: The pipe is elongated through a reducing machine to achieve the desired dimensions.
The mandrel mill technique produces seamless, smaller-diameter pipes with great dimensional accuracy. The method ensures precise dimensions and a smooth interior surface. This process is actually faster than the mannesman plug mill pipe manufacturing process.
Mannesmann Plug Mill Pipe Manufacturing Process
This manufacturing process is named after its inventor, Heinrich Mannesmann. He is a German engineer who discovered the process in the late 19th century. This manufacturing process uses multiple tools and piercings. The method includes the following stages.
- Piercing & Elongating: A conical, rotating piercer or plug pierces the heated billet. It gradually elongates and shapes it into a seamless steel tube.
- Rolling(plug mill): The process then again uses another plug mill to refine its dimensions further.
- Reeling & Sizing I: Then, the process reels & sizes the pierced tube to achieve the desired dimensions & thickness.
- Cooling & straightening: The elongated & sized tube is cooled & straightened for uniformity.
- Heat treatment & sizing II: After heat treatment, the process is further sized to ensure the pipe’s mechanical properties. This step continues to meet the required specifications.
Mannesmann plugs mill process is suitable for manufacturing seamless pipes with larger diameters. This process also ensures improved structural integrity by employing repeated piercing. This multiple-piercing method refines the pipe’s dimensions and enhances its mechanical properties.
Forged Seamless Pipe Manufacturing Process
This manufacturing process involves heating and forcing a steel billet through a shaped die. Finally, the result is the formation of a seamless steel tube. However, this manufacturing process is suitable for achieving complex cross-sectional shapes. In addition, they are famous for creating excellent surface finish. The method involves the following steps:
- Forging: This step uses forging equipment to apply appropriate forces. Forging involves molding the material into the appropriate pipe shape. It usually entails the use of dies or molds.
- Sizing & Reduction: The forged metal is then further sized and reduced to achieve the desired dimensions & thickness. This step contributes to the final mechanical properties of the seamless pipe.
- Heat Treatment: The pipe undergoes heat treatment to optimize its microstructure & mechanical characteristics. This step also enhances the overall strength, durability, and resistance to corrosion.
Extrusion Processes
The extrusion process in seamless pipe manufacturing offers versatility in pipe shapes & dimensions. It is also a more cost-effective solution than other methods. This method is suitable mainly for small to medium-sized steel pipe fabrication. The extrusion process includes the following manufacturing steps:
- Extrusion through the die: The heated billet is forced through a shaped die. The result is forming a seamless steel tube with the desired outer diameter & characteristics.
- Elongation: The extruded tube undergoes elongation. It is a process that increases its length while enhancing its mechanical properties.
Welded Steel Pipe Fabrication Process
Welded stainless steel pipes are also used in a wide variety of different fields. They are extensively used for structural applications in the construction industry. They are also popular for transferring various gases and liquids. In addition, welded pipes are renowned in the food and beverage industries for their smooth and easy-to-clean surfaces. Furthermore, these stainless steel pipes are used in various sectors.
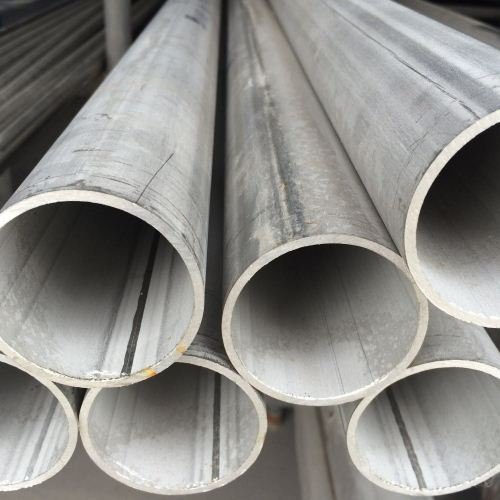
The steel pipe fabrication process for welded steel pipe also has four primary types. Different manufacturing industries use specific fabrication methods based on their varying requirements. The common procedure can be observed in all four following welded stainless steel pipe fabrication methods.
- Uncoiling & Leveling: All the processes below start with uncoiling the steel. These raw materials typically come in the form of a coil. The leveler then levels these coils and prepares for further fabrication.
- Slitting & Recoiling: Uncoiled steel is slit according to pipe diameter. Later, the process recoils the slitted steel for better manageability & further processing.
- Slitted steel uncoiling & leveling: These slitted steel coils go to different manufacturing plants. Each process then begins by uncoiling the slitted steel & labeling it for the later stage.
- Roll & gage forming: These flat steel plates are subjected to roll & gage forming processes. This process shapes the slitted plate into the desired pipe form.
Moreover, the post-processing steps are similar in all four stainless steel fabrication methods. They are:
- Post-annealing: After welding, the welded steel pipes undergo post-annealing processes. It is a heat treatment process that enhances steel properties.
- Cooling & sizing: The pipes are then cooled. Later, the sizing process is implemented to set structures, ensuring that they meet specific dimensions.
- Straightening & end facing: The final steps involve straightening the pipes for uniformity. In addition, end-facing is applied for smooth and even surfaces.
Electric Resistance Welding (ERW)
ERW is a popular method for welding steel pipes. It involves the use of an electric current to generate heat. This certain level of heat causes the steel edges to fuse together. The welded joint is created without the need for filler material.
However, ERW is popular for its efficiency & versatility. As a result, they are highly suitable for both thin & thick-walled pipes. These pipes find widespread application in various industries, including construction & transportation.
Electric Fusion Welding (EFW)
EFW is a remarkable pipe welding method used mostly for larger pipe diameters. The process is also referred to as electron beam welding. It uses the high-speed movement of the electron beam directed to the edges. The kinetic energy from these movements produces extreme heat and makes the workpiece melt. The result is the formation of the weld.
EFW is famous for its ability to produce high-quality welds with excellent mechanical properties. The process can be applied to a wide range of materials and is particularly effective for welding stainless steel and alloy pipes. One of the great advantages of EFW is the ability to handle thicker pipes. As a result, they are popular in applications in heavy industries such as oil & gas.
High-frequency welding (HFW)
HFW utilizes high-frequency current to create heat for joining steel pipes. Normally, they use a higher frequency than ERW. Typically, the range starts from more than 70 kHz. This steel pipe fabrication method is suitable for welding thick sections of steel. Therefore, it has become a common choice for manufacturing pipes used in heavy-duty applications.
HFW steel fabrication process offers excellent weld quality and high production rates. Another great advantage of this process is its applicability to a variety of steel grades. HFW pipe is widely used in oil & gas transportation, oil well pipelines, and building structures. They are also prevalent in various kinds of mechanical pipes and ship-building accessories.
Submerged Arc Welding (SAW)
SAW typically has two primary types. One of the Long Seams (LSAW) and SPPiral/ Helical Seams (SSAW/HSAW). The LSAW Pipe (Longitudinal Submerges Arc-Welding Pipe) fabrication process uses the steel plate as a raw material. It molds it by the molding machine and then does double-sided submerged arc welding.
HFW steel fabrication process offers high welding speeds and deep penetration. They can handle large-scale production as well.
Conclusion
Let’s wrap everything up! There are many different kinds of steel pipe fabrication techniques. These varieties may alter depending on numerous factors such as material properties and budget. All of these fabrication procedures are common in a variety of sectors. However, this article evaluated many seamless and welded stainless steel pipe manufacturing methods. One of four stainless steel fabrication procedures can make each of these pipes.
We hope that the article has demonstrated the many varieties of stainless steel fabrication methods. It can also assist you in determining the best stainless steel pipe for your project. However, if you require any additional support, please do not hesitate to contact us.