In every engineering process, casting defects are a frequent occurrence. Any approach has certain limitations that result in flaws. You can achieve a defect-free cast via proper design and moulding, but control rules and human intervention cause most faults. We can reduce casting flaws with the right help on the job.
In general, a good casting product will have some flaws. Therefore the foundry business is working to reduce these flaws. Non-destructive testing techniques such as ultrasonic, radiography, magnetic particle, die penetration, and others may detect these casting flaws. Today, we\’ll look at several typical casting flaws, their causes, and how to fix them.
Types of Casting Defects
A variety of factors may cause many kinds of faults. Some of the remedies to one type of flaw may create a different type of problem. This section will illustrate the most common types of casting defects encountered in metal casting processes.
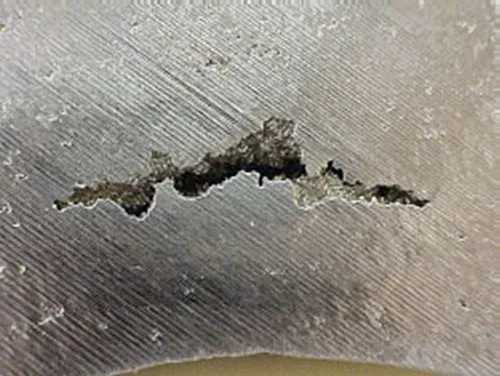
Shrinkage casting Defects
Solidification shrinkage occurs when metal transitions from a liquid to a solid, while thermal contraction occurs as it cools to room temperature. Consequently, the study includes shrinkage allowances in the design of cast components to ensure that they achieve the required dimensions.
For example, cast steel shrinks at a rate of 14 inches per foot, resulting in rough-looking castings. Shrinkage tolerances for different metals are known, and an expert mould designer will account for shrinkage while constructing a mould.
Shrinkage may also contribute to problems in cast goods, such as failure and leaking. Sometimes you may see these flaws on the casting surface and visually identify them through dye penetrants or other non-destructive methods. Internal casting flaws are often challenging to detect and need X-ray examination or destructive testing. The term \”open- and closed-shrinkage faults\” refers to both types of problems.
Open shrinkage casting defect
Pipes may develop on the surface and extend into the body of the casting if the metal cools and shrinks without enough liquid to fill any holes. Similarly, the study refers to the surface flaws as cave defects or sinks that extend over the face. It exposes the defects to the environment in both cases, and air replaces the molten metal.
In the last phases of solidification, cracks and scorching tears are common. You may see them around sudden changes in stress concentration, such as a thin web linking two heavy portions. They may also happen in plump cells where heat pools and when there is a partial preliminary draft.
The casting sprue, which is the channel through which the machine pours molten metal into a mould, is the most frequent source of shrinkage. The metal takes longer to contract and solidify in certain places, such as the heavier portions of the mould, reducing feed material availability and increasing the probability of shrinkage, mainly if the sprue is too narrow for the amount of flow. A correctly sized sprue connected directly to the heavy section may fill the shrinkage hole and supply the feed material required to counter shrinkage as the section cools. Furthermore, utilizing a rounded gate on the sprue rather than a flat or square gate may decrease the chance of developing flaws.
Closed shrinkage casting defects
Porosity is one of the most common flaws in castings, and the defects come from the trapped gases in the molten metal and shrinkage when the casting cools. The most frequent form of porosity is shrinkage porosity, typically visible on the surface of a cast component as tiny holes or fractures. Although these holes seem spherical, they are angular in shape and likely to develop interior branching cracks.
Such shrinkage is particularly common in thick multi-angled components when the metal cools and hardens in a non-uniform pattern. Porosity may occur inside of casting without showing up on the part\’s surface. When solidified metal surrounds liquid metal, molten metal cannot fill behind the liquid as it cools and shrinks, resulting in this defect.
Prevention
Using a thin or tapered sprue, you may spray the molten metal instead of poured into the cavity. When this occurs, portions of the workpiece begin to harden before it fills the mould. The molten flow into the pit should be as consistent as possible, and a more prominent central sprue or multiple-sprue arrangement may assist with this.
The process utilizes risers to guarantee enough molten material to fill gaps when the component solidifies and shrinks. The size of the ribs should be such that they are the last to freeze. Sometimes add insulation to achieve this.

Gas porosity
trapped air and vapours may cause porosity on the surface or within the casting. Unlike the solid form, the molten metal may retain a large amount of dissolved gas, resulting in gas porosity. When a consequence, as the substance cools, gas bubbles develop. During the casting process, turbulence may potentially introduce gasses. This flaw arises when molten metal is put into the mould too fast.
Poor venting of moulds and cores and insufficient drying of moulds and cores cause gas porosity.
Pinholes
Outside the casting or below the flake\’s surface, nodular or compacted graphite iron, malleable cast iron, and cast steel castings are the most likely to have bubbles or voids.
Pinholes may develop in small clusters or across a wide region, damaging any casting portion. They are sometimes not apparent until after machining, although they are always visible to the naked eye.
Pinholes may appear as nodular bare metal bubbles or bubbles with graphite skins or more extensive irregularly shaped cavities followed by slags or oxidation.
Open holes
These blowholes are visible on the cast\’s surface and are simpler to spot than subterranean blowholes.
Prevention
Before the liquid pour, a good mould design may reduce gas porosity or inject nitrogen into the aluminium alloy. Hipping may also be used to remove tiny quantities of porosity from the inside of the casting. The process places the casting in a high-temperature furnace and contains in a pressurized container in this technique. The casting is subsequently heated in an inert gas, most frequently argon, to remove the porous components by applying isostatic pressure.
To melt metal in a vacuum, in an atmosphere with low-solubility gases, or under a flux that inhibits contact with the air, first include excellent fluxing and melting techniques. Second, increase the gas permeability of coarser, greater permeability sands. Following that, increased mould and core permeability enable air and gas to escape from the mould cavity. Finally, dry out moulds and cores before using them, keep them dry, and reduce the metal temperature during casting to increase the pace of solidification.
Pouring metal casting defects
During the pouring of metal into the mould, faults may occur. A pouring metal fault will fall into one of the following categories. Misruns, cold shuts, and inclusions are common pouring metal faults.

Cold shut
A cold shut is a surface defect that appears as a line or fracture on the casting surface with a circular edge. This flaw is apparent to the human eye, and it causes the cast to reject, resulting in a weak area.
The streams of molten metal entering the mould from two gates will meet at a junction. Low temperatures at the junction may impede fusion, causing the streams to harden before fusing, resulting in a cold shut.
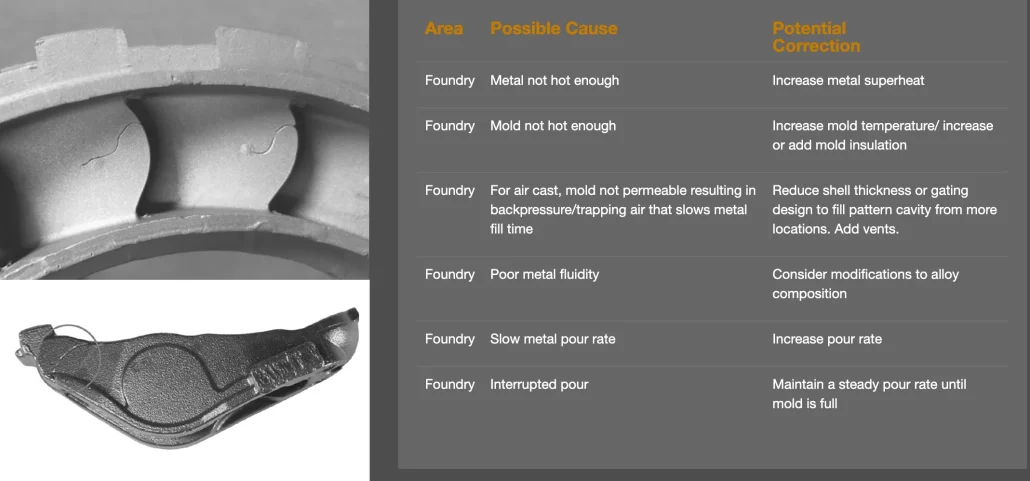
A lack of fluidity in the molten metal or a poorly designed gating system is the most common cause of cold shut. The easiest method to avoid hard closes is to make the molten metal more fluid. You may carry this technique in a variety of ways. First, optimize the gating mechanism to reduce narrow cross-pathways and keep flow paths short. Second, to avoid premature solidification, raise the pouring temperature. Third, increase the mould’s gas permeability.
Misruns
Cold closes and misruns have a lot in common. Misruns happen when the liquid metal is too cold to flow to the mould cavity\’s edges before freezing and hardening. The liquid metal does not fill the chamber of the mould. The misruns are the parts of the mould, and the mould doesn’t fill it.
Premature solidification occurs for the same reasons that cold shut occurs. Check the mould design, gating system design, and molten metal fluidity if you have misruns.
Cold Shots
Solid globules may develop if a liquid splatters while being poured. These globules get caught in the casting when they freeze. The process forms cold shots like a ball, a drop, or a pearl and connects only to the metal.
Consider changing pouring processes to decrease turbulence and tweaking gating system designs to lower gate speed to avoid splattering and cold shots.
Inclusion
On the casting surface, you may observe these uneven metallic crusts. Scabs are just a few centimetres thick, yet they are visible to the naked eye. Sharp edges, irregular forms, and a strong connection to the casting are common characteristics.
Scabs and rat tails are closely linked, and they often occur together. This process usually removes the scabs to expose a rat tail. When molten metal containing slag particles is injected into the mould cavities and hardens, slag inclusion occurs.
You may avoid slag inclusion with a simple change. Before putting the molten metal into the mould cavity, remove any slag particles.
You may remove slag metal by treating it with flux in a vacuum or an inert environment. Additionally, you may accomplish this by adding chemicals to the mixture to induce slag to float to the top, where it will be easy to detect and remove before pouring. Alternatively, you may use a special ladle that pours metal from the bottom. Finally, including a ceramic filter into the gating system may be beneficial.

Metallurgical casting Defects
This kind of casting flaw is prevalent in steel casting techniques. You\’ll mostly come across two metallurgical types of flaws.
Hot tears
Cracks appear as uneven fissures arranged in a branching pattern. You may notice some cracks are apparent without magnification, while others may need them. As the casting cools near the conclusion of solidification, shots occur.
Hot tears will emerge if the forming metal is not strong enough to withstand tensile stresses during solidification. Poor mould design is the primary cause of hot tears. You may efficiently resolve these problems by modifying the mould to enhance collapsibility.
Hard Spots
Hot spots are areas that are more difficult than the rest of the region. This situation is because they cooled faster than the surrounding material. Hard areas may obstruct machining and lead to increased tool wear.
Hot spots are a direct consequence of insufficient cooling. If hot spots are a concern for you, there are two options. First and foremost, adjust the cooling technique. Second, consider altering the chemical makeup of the metal.