When it comes to cold vs hot forging, we all make mistakes understanding the differences. In this context, we must first understand what forging involves. And then at the later part of the article, we will state the most common cold forging vs hot forging differences.
The process of forging involves heating, deforming, and finishing a piece of metal. This process uses the force of a falling ram on an anvil or a die press enclosing a piece of metal and squeeze-forming the component to forge materials into bespoke forms.
Forgings can tolerate severe pressure and preserve structural integrity under stress because the grains of metal realign when heated and bent.
What is Cold Forging
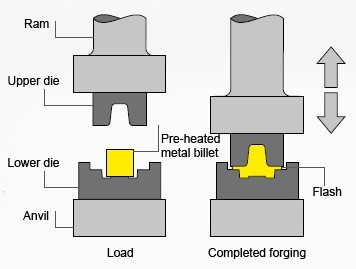
Cold forging can take numerous forms, such as cold heading, bending, and cold drawing, to produce a wide range of items. The die material and form, the workpiece material, the lubricant, and the temperature are essential aspects of the cold forging process.
Usually, the cold forging happens at room temperature or at a temperature where the microstructure of the metal does not change. It\’s a compressive method in which the process plastically shapes metal workpieces by compressing them between contoured dies.
The process begins with a chemically lubricated press the bar slug under extremely high pressures within a closed die. After that, the metal flows and takes on the appropriate form.
Cold forging materials can range from low-end alloys and carbon steels through 300 and 400 series stainless steel, chosen aluminum alloys, bronze, and brass.
Application of Cold Forging
When the process needs 10 lbs or less to forge the weight of the cold forging pieces, the procedure is most cost-effective. It takes priority when integral design components such as built-in flanges and implementation of bosses.
Cold forgings are widely popular in the automotive sector manufacturing to produce steering and suspension components, anti-lock brake systems, axles, bits, clutch hubs, gears, pinions, pins, step, and intermediate shafts, and sleeves.
Cold Forging Process
- First, this process lubricates the workpiece before forging to prevent it from the die adhering and keep it cold throughout the forming process, as deforming can yield temperatures ranging from 250° to 450°.
- Second, Put the metal component on a die that has the final part\’s form. You might divide the die into two parts, one linked to the hammer and the other under the workpiece. The hammer is the top component of the metal piece and the striking mechanism that generates the force to bend it.
- Third, accomplish the hitting of the workpiece or stroke using one of three mechanisms: hydraulic, pneumatic, or mechanical. Each technique sends a shaft with the hammer on it down at considerable force onto the workpiece to generate the required form.
- Fourth, Flash is an extra metal that is present around a die or group of dies. It protrudes from the forging\’s body as a thin plate where it removes the dies meet and during trimming. Flash restricts the flow of metal, resulting in a precise imprint.
- Fifth, determine the manner of removing the component on the type of procedure. Most modern factories employ automation, such as a conveyor or robotic hand, to remove the item. Another cost-cutting strategy eliminates the need for material handling.
- Finally, like other aspects of the process, it can take a variety of shapes. Cut and deliver the quantity to shipping for situations that need only one die and one stroke. After that transfer, the parts with numerous aspects to various die operations for feature addition.
Pros and Cons
Common advantages
- Preprocessing, temperature, and finishing all contribute to the cheap cost of cold forging. Other methods of metal shaping necessitate some form of preprocessing, such as heating the workpiece.
- Once you processed a workpiece in cold forging, it is complete and requires minimal finishing, which reduces labor costs.
- Because there is very little waste and scrap, cold forging can save up to 70% of production costs in terms of materials.
- Cold forging is a simple process that involves placing the workpiece directly into the forging machine, which produces a finished part almost instantly.
- The elimination of heat requirements is the primary reason for cold forging\’s environmental friendliness since furnace gases and smoke causes significant carbon emissions.
- Cold forging improves products\’ performance by rearranging the workpiece\’s grain structure to match the final part\’s configuration.
- Working with metal can lead to a slew of issues. By raising the overall strength of the metal and minimizing the possibility of material integrity loss, cold forging avoids some of the negative impacts, such as porosity fatigue.
- Cold forged parts can withstand a lot of pressure. The workpiece may keep its revised form even when pushed beyond its yield or elastic limit.
Other benefits
- Throughout a manufacturing run, it maintains critical and close tolerances of parts. They have meticulously recreated to the point that each component is an identical replica of the original.
- Cold forging, unlike other procedures, provides for creative flexibility, allowing for the creation of complicated curves and forms that would otherwise need several distinct and expensive secondary methods.
- Cold forging, unlike other procedures, provides for creative flexibility, allowing for the creation of complicated curves and forms that would otherwise need several distinct and expensive secondary methods.
- Although there are differences in cold forging production processes, the high manufacturing speed of cold forging can create up to 400 pieces per minute. The only factor that affects the process\’s speed is the part\’s size.
- Forging is possible with various metals, including hard metals such as carbon steel, alloy steel, stainless steel, and soft metals such as aluminum, brass, and copper.
Disadvantages
- Cold forging isn\’t flawless. Like any production process, there are limits and drawbacks to cold forging that you will need to examine before adopting it for your next production project.
- You can manufacture only primary forms and patterns in great numbers. You can\’t make unique or complicated designs through cold forging. Deformation levels and shaping grades are restricted, and cold-forged metals have reduced flexibility.
- The change of the grain structure of metal offers it greater strength but may cause residual stress.
- Certain types of cold forging need heat treatments to remove any fractures or creep hardening.
- There is a restriction to the sorts of metals that can be cold forged. You should not select ones with poor plasticity and susceptibility to strain to harden as they lose their elasticity and will break under tensile stress. Only metals having a hardness of HRC 44 on the Rockwell scale may be utilized.
- Production operations need a considerable quantity of force to provide the required compressive strength and pressure. Though the inclusion of hydraulics and pneumatics has lessened the size of the equipment, it has not removed the amount of power the machines use.
- Tools die, and molds must be carefully developed, durable, and powerful enough to sustain continual repeating stress.
What is Hot Forging
Heat the metal above its recrystallization temperature for hot forging. This process reduces the flow stress and energy needed to produce the metal, allowing the pace of production to increase (or strain rate). Hot forging makes it simpler to form the metal and makes it less prone to fracture.
Standard temperatures for hot forging includes: Aluminum (Al) Alloys – 360° (680°F) to 520°C (968°F); Copper (Cu) Alloys – 700°C (1 292°F) – 800°C (1 472°F); Steel – up to 1 150°C (2 102°F)
Application of hot forging
Usually, Ho forging uses high temperatures in the recrystallization process. The method improves formability and enables the fine-grained microstructure to be adjusted. Hot forging, more than any other forming method, is known for its tremendous strength and longevity.
It will also allow hot die forging in situations where high operational loads need specialized component requirements. You can refer to these parts as \”Safety-Critical Parts\”. The automobile and aerospace industries are the primary buyers of hot forgings.
Hot Forging Process
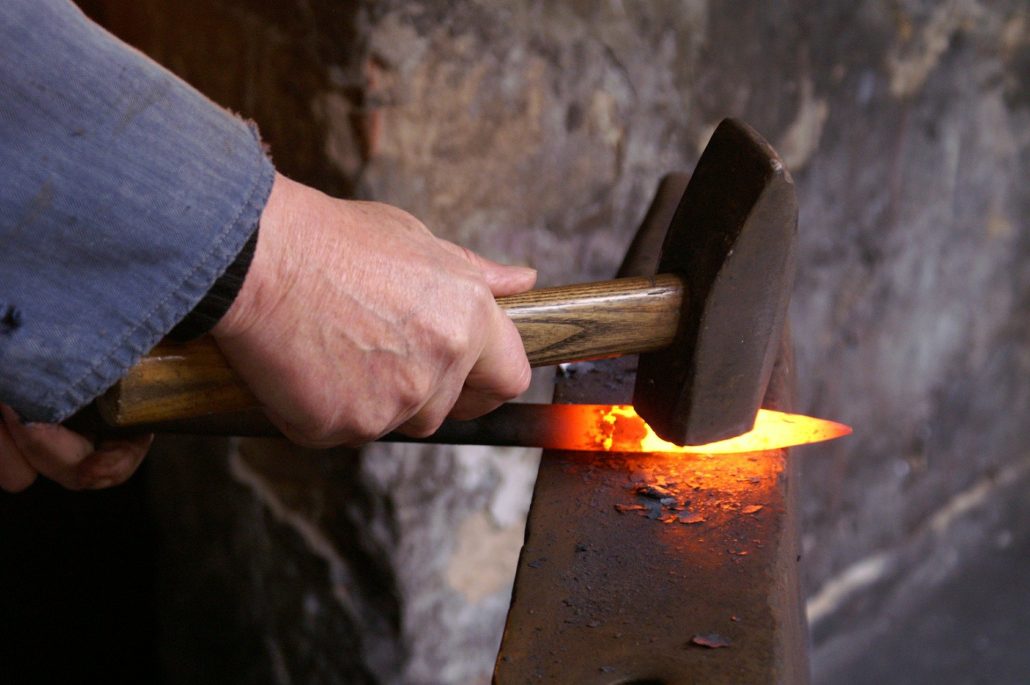
First, carry the hot forging process at the most significant temperature possible without destroying the metallurgical properties of the alloy (up to 1250°C for steel, 300 to 460°C for Al-Alloys, 750 to 1040°C for titanium alloys, and 700 to 800 °C for Cu-Alloys).
Second, recrystallization happens at the same time as deformation, eliminating strain hardening. Consequently, and for optimal results, the forging temperature must be kept above a certain minimum during the whole operation, depending on the alloy.
This condition also eliminates the potential of a lack of enforceability, leading to fractures since it diminishes the flexibility at lower temperatures. After timing, The forging procedure stays below these temperature restrictions.
Fourth, If the process does not finish forging when it reaches the lower limit, reheating is required if possible. Otherwise, treat the item as forged and finish it in a different way. Because the temperature interval required for the hot forging process is so critical, all toolings are warmed to prevent the component from losing temperature during the forging stage.
This method led to an exact and precise closed die forging technology known as \”isothermal forging.\”
Fifth, Keep heating the tools (really dies) at the desired forging temperature during isothermal forging. However, depending on the material and hence the forging temperature, this notion is implemented in various ways. The die material must maintain the high mechanical characteristics necessary to deform the component material at the forging temperature.
Sixth, the isothermal process can vary materials to materials, such as:
- Because aluminum cools fast and the forging temperature is low, it is a must for aluminum forging: all die grades must maintain the requisite mechanical qualities.
- It is achievable for copper and titanium alloys if the dies consist of a sophisticated (and costly) quality.
- For steel alloys, where very few materials die to hold at 1250 °C forging stress, it is challenging.
As a result, isothermal forging is uncommon for titanium alloys. And, highly secretive for steel and nickel-based alloys (dedicated to the highest difficult turbine disks for jet engines, for instance.)
Pros and Cons
Advantages
- The main benefit of hot forging is that the recrystallization process eliminates the strain-hardening effects when the metal is deformed.
- Parts have higher elasticity, making them suitable for a wide range of applications.
- Grain Structure with Homogenization
- The lack of porosity allows for a wide variety of finishing procedures such as polishing and surface treatment
- When dealing with stricter metals like steel, this is an efficient technique.
Disadvantages
- Tolerances are less exact.
- Warping of the material during the cooling process is a possibility.
- Metal grain structure varies.
- Possible interactions between the metal and the environment (scale formation)
Cold forging vs Hot forging
Cold forging vs hot forging is a very important topic to discuss nowadays. The contribution of these two processes is enormous. The temperature difference between hot and cold forging is different. The cold forging stresses and strains metals at ambient temperature. On the other hand, hot forging warms metals near or at their melting temperatures.
Recrystallization is the key to the temperature range. Cold forging occurs before recrystallization, while hot forging occurs after recrystallization.
Based on the following factors, The decision between cold and hot forging are:
- Fabricators\’ equipment and machining: To get the most out of their equipment, producers specialize in one technique or the other.
- Customer demand: Engineers decide on the optimal procedure to generate their ideas during the design phase of component creation.
- Types of components produced: The component\’s design often determines the limitations in selecting the appropriate technique, as specific parts can only be hot forged. In contrast, others are ideal for cold forging. Cold forged components have basic designs with few complicated details, but hot-forged members may have incredibly exact microscopic minute elements.
Manufacturers prefer cold forging wherever feasible since it needs less equipment and does not include heating, lowering manufacturing costs substantially.
Summary
The process of forging involves heating, deforming, and finishing a piece of metal. Two types are forging cold forging, and hot forging.
Cold forging can take numerous forms, such as cold heading, bending, and cold drawing, to produce a wide range of items. On the other hand, hot forging happens by heating the metal above its recrystallization temperature for hot forging.
We have stated the common cold forging vs hot forging differences between the cold forging and hot forging processes. We hope we could mention the specific differences among them.