Когда речь заходит о холодной и горячей ковке, мы все ошибаемся, понимая разницу. В этом контексте мы должны сначала понять, что включает в себя ковка. А затем, в дальнейшей части статьи, мы укажем наиболее распространенные различия между холодной и горячей ковкой.
Процесс ковки включает в себя нагрев, деформацию и отделку куска металла. В этом процессе используется сила падающего на наковальню плунжера или штамповочного пресса, заключающего в себе кусок металла и выдавливающего деталь, чтобы придать материалу требуемую форму.
Поковки могут выдерживать сильное давление и сохранять структурную целостность под нагрузкой, поскольку зерна металла выравниваются при нагревании и изгибе.
Что такое холодная ковка
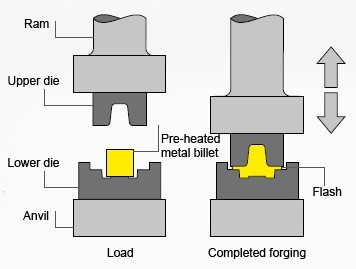
Холодная ковка может принимать различные формы, такие как холодная штамповка, гибка и холодное волочение, для производства широкого спектра изделий. Материал и форма штампа, материал заготовки, смазка и температура являются важнейшими аспектами процесса холодной ковки.
Обычно холодная ковка происходит при комнатной температуре или при температуре, при которой микроструктура металла не изменяется. Это\ метод сжатия, при котором металлические заготовки пластически формируются путем сжатия между контурными штампами.
Процесс начинается с прессования прутка с химической смазкой под чрезвычайно высоким давлением в закрытой матрице. После этого металл течет и принимает нужную форму.
Материалы для холодной ковки могут варьироваться от низкоуглеродистых сплавов и углеродистых сталей до нержавеющей стали серий 300 и 400, избранных алюминиевых сплавов, бронзы и латуни.
Применение холодной ковки
Когда для ковки требуется 10 фунтов или меньше веса изделий холодной ковки, эта процедура является наиболее экономически эффективной. Она имеет приоритет при создании цельных конструктивных элементов, таких как встроенные фланцы и выполнение бобышек.
Холодная штамповка широко распространена в автомобильной промышленности для производства компонентов рулевого управления и подвески, антиблокировочных тормозных систем, осей, насадок, ступиц сцепления, шестерен, пальцев, ступенчатых и промежуточных валов, втулок.
Процесс холодной ковки
- Во-первых, при этом процессе заготовка перед ковкой смазывается, чтобы предотвратить ее прилипание к штампу и сохранить ее холодной в течение всего процесса формовки, так как при деформации температура может достигать 250-450°.
- Во-вторых, поместите металлическую деталь в штамп, имеющий окончательную форму детали\. Можно разделить штамп на две части, одна из которых связана с молотом, а другая находится под заготовкой. Молот - это верхняя часть металлической детали и ударный механизм, который создает усилие для ее сгибания.
- В-третьих, удар по заготовке или удар осуществляется с помощью одного из трех механизмов: гидравлического, пневматического или механического. Каждый из них направляет вал с молотком вниз со значительной силой на заготовку, чтобы создать требуемую форму.
- В-четвертых, флэш - это дополнительный металл, который присутствует вокруг штампа или группы штампов. Он выступает из корпуса ковки\ в виде тонкой пластины в местах соприкосновения штампов и во время обрезки. Флеш ограничивает поток металла, в результате чего получается точный оттиск.
- В-пятых, определите способ удаления компонента по типу процедуры. На большинстве современных заводов для извлечения деталей используется автоматика, например конвейер или роботизированная рука. Еще одна стратегия снижения затрат - отказ от погрузочно-разгрузочных работ.
- Наконец, как и другие аспекты процесса, он может принимать самые разные формы. В ситуациях, когда требуется только один штамп и один ход, детали разрезаются и доставляются на доставку. После этого детали с многочисленными аспектами передаются на различные операции штамповки для добавления элементов.
Плюсы и минусы
Общие преимущества
- Предварительная обработка, температура и финишная обработка - все это обусловливает дешевизну холодной ковки. Другие методы формовки металла требуют определенной предварительной обработки, например, нагрева заготовки.
- После обработки заготовки холодной ковкой она полностью готова и требует минимальной доводки, что снижает трудозатраты.
- Поскольку отходов и лома очень мало, холодная ковка позволяет сэкономить до 70% производственных затрат на материалы.
- Холодная ковка - это простой процесс, при котором заготовка помещается непосредственно в ковочный станок, который практически мгновенно производит готовую деталь.
- Отсутствие потребности в тепле является основной причиной экологичности холодной ковки\, поскольку печные газы и дым вызывают значительные выбросы углерода.
- Холодная ковка улучшает характеристики изделий\, перестраивая зернистую структуру заготовки\ в соответствии с конфигурацией конечной детали\.
- Работа с металлом может привести к целому ряду проблем. Повышая общую прочность металла и сводя к минимуму возможность потери целостности материала, холодная ковка позволяет избежать некоторых негативных последствий, таких как усталость от пористости.
- Детали, изготовленные методом холодной ковки, могут выдерживать большое давление. Заготовка может сохранять свою измененную форму даже при нагрузке, превышающей предел текучести или упругости.
Другие преимущества
- На протяжении всего производственного цикла сохраняются критические и близкие допуски деталей. Они скрупулезно воссозданы до такой степени, что каждый компонент является точной копией оригинала.
- Холодная ковка, в отличие от других процедур, обеспечивает творческую гибкость, позволяя создавать сложные изгибы и формы, которые в противном случае потребовали бы нескольких отдельных и дорогостоящих вторичных методов.
- Холодная ковка, в отличие от других процедур, обеспечивает творческую гибкость, позволяя создавать сложные изгибы и формы, которые в противном случае потребовали бы нескольких отдельных и дорогостоящих вторичных методов.
- Несмотря на различия в производственных процессах холодной ковки, высокая скорость производства позволяет создавать до 400 деталей в минуту. Единственным фактором, влияющим на скорость процесса\, является размер детали\.
- Ковка возможна с различными металлами, включая твердые, такие как углеродистая и легированная сталь, нержавеющая сталь, и мягкие, такие как алюминий, латунь и медь.
Недостатки
- Холодная ковка не безупречна. Как и у любого производственного процесса, у холодной ковки есть свои ограничения и недостатки, которые необходимо изучить, прежде чем использовать ее в своем следующем производственном проекте.
- Вы можете производить только первичные формы и узоры в большом количестве. Холодная ковка не позволяет создавать уникальные или сложные конструкции. Уровни деформации и степени формообразования ограничены, а металлы, полученные холодной ковкой, обладают пониженной гибкостью.
- Изменение зерновой структуры металла обеспечивает ему большую прочность, но может вызвать остаточные напряжения.
- Некоторые виды холодной ковки нуждаются в термической обработке для устранения трещин и ползучей закалки.
- Существует ограничение на виды металлов, которые можно подвергать холодной ковке. Не следует выбирать для закалки металлы с низкой пластичностью и восприимчивостью к деформации, так как они теряют эластичность и ломаются при растяжении. Можно использовать только металлы с твердостью HRC 44 по шкале Роквелла.
- Производственные операции требуют значительных усилий для обеспечения требуемой силы сжатия и давления. Хотя применение гидравлики и пневматики позволило уменьшить размеры оборудования, оно не устранило потребляемую машинами мощность.
- Инструменты, штампы и пресс-формы должны быть тщательно разработаны, прочны и достаточно мощны, чтобы выдерживать постоянные повторяющиеся нагрузки.
Что такое горячая ковка
Для горячей ковки нагрейте металл выше температуры его рекристаллизации. Этот процесс снижает напряжение потока и энергию, необходимую для производства металла, что позволяет увеличить темп производства (или скорость деформации). Горячая ковка упрощает формовку металла и делает его менее склонным к разрушению.
Стандартные температуры для горячей ковки включают: сплавы алюминия (Al) - от 360° (680°F) до 520°C (968°F); сплавы меди (Cu) - 700°C (1 292°F) - 800°C (1 472°F); сталь - до 1 150°C (2 102°F).
Применение горячей ковки
Обычно при ковке Ho в процессе рекристаллизации используются высокие температуры. Этот метод улучшает формуемость и позволяет регулировать мелкозернистую микроструктуру. Горячая ковка, как никакой другой метод формовки, известна своей огромной прочностью и долговечностью.
Это также позволяет использовать горячую штамповку в ситуациях, когда высокие эксплуатационные нагрузки требуют специальных требований к деталям. Такие детали можно назвать \"критически важными деталями\". Автомобильная и аэрокосмическая промышленность являются основными покупателями горячих штамповок.
Процесс горячей ковки
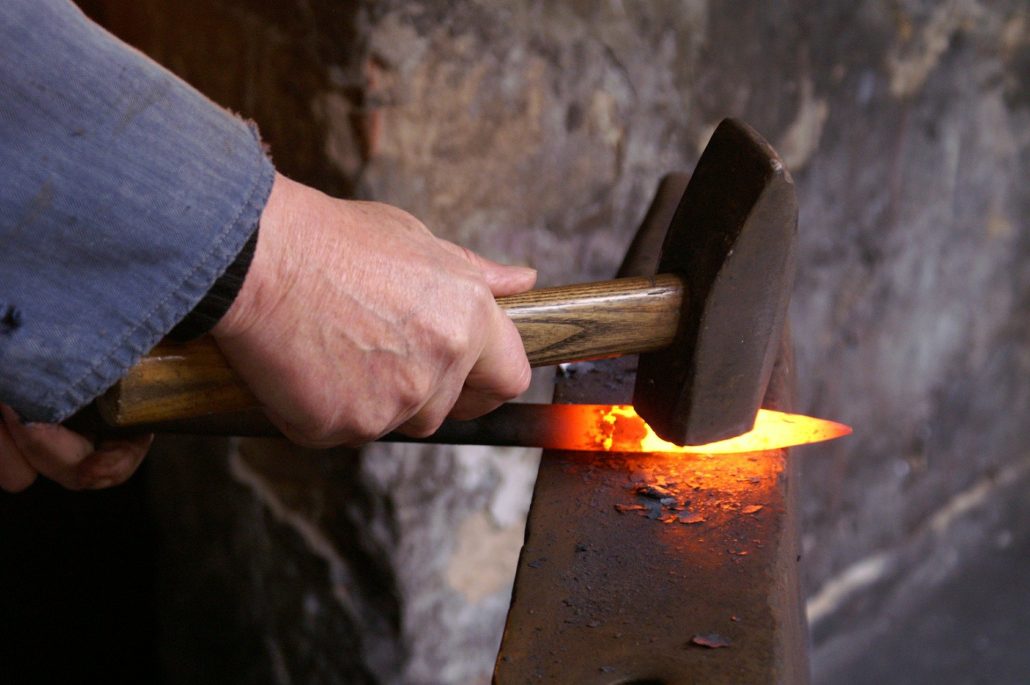
Во-первых, процесс горячей ковки следует проводить при максимально возможной температуре без разрушения металлургических свойств сплава (до 1250°C для стали, от 300 до 460°C для Al-сплавов, от 750 до 1040°C для титановых сплавов и от 700 до 800°C для Cu-сплавов).
Во-вторых, рекристаллизация происходит одновременно с деформацией, что исключает деформационное упрочнение. Следовательно, для достижения оптимальных результатов температура ковки должна поддерживаться выше определенного минимума в течение всей операции, в зависимости от сплава.
Это условие также исключает возможность недостаточной прочности, приводящей к переломам, поскольку при более низких температурах гибкость снижается. После определения времени процедура ковки остается ниже этих температурных ограничений.
В-четвертых, если процесс не завершает ковку, когда она достигает нижнего предела, необходимо провести повторный нагрев, если это возможно. В противном случае следует рассматривать изделие как кованое и обрабатывать его другим способом. Поскольку температурный интервал, необходимый для процесса горячей ковки, настолько критичен, вся оснастка нагревается, чтобы предотвратить потерю температуры детали на этапе ковки.
Этот метод привел к созданию точной и прецизионной технологии ковки в закрытых штампах, известной как \"изотермическая ковка.\"
В-пятых, во время изотермической ковки поддерживайте нагрев инструментов (на самом деле штампов) при требуемой температуре ковки. Однако в зависимости от материала и, соответственно, температуры ковки это понятие реализуется по-разному. Материал штампа должен сохранять высокие механические характеристики, необходимые для деформации материала детали при температуре ковки.
В-шестых, изотермический процесс может отличаться от материала к материалу, например:
- Поскольку алюминий быстро остывает, а температура ковки низкая, это обязательное условие для ковки алюминия: все марки штампов должны сохранять требуемые механические качества.
- Это достижимо для медных и титановых сплавов, если штампы отличаются высоким (и дорогостоящим) качеством.
- Для стальных сплавов, где очень немногие материалы выдерживают штамповку при напряжении 1250 °C, это является сложной задачей.
В результате изотермическая ковка редко применяется для титановых сплавов. А для стали и сплавов на основе никеля (например, для сложнейших дисков турбин реактивных двигателей) - весьма секретная.
Плюсы и минусы
Преимущества
- Основное преимущество горячей ковки заключается в том, что процесс рекристаллизации устраняет эффект деформационного упрочнения при деформации металла.
- Детали обладают повышенной эластичностью, что делает их пригодными для широкого спектра применения.
- Зернистая структура с гомогенизацией
- Отсутствие пористости позволяет выполнять широкий спектр отделочных процедур, таких как полировка и обработка поверхности
- При работе с такими прочными металлами, как сталь, это эффективная техника.
Недостатки
- Допуски менее точны.
- Существует вероятность деформации материала в процессе охлаждения.
- Структура зерна металла различна.
- Возможные взаимодействия между металлом и окружающей средой (образование накипи)
Холодная ковка против горячей ковки
Холодная ковка и горячая ковка - очень важная тема для обсуждения в настоящее время. Вклад этих двух процессов огромен. Разница температур между горячей и холодной ковкой различна. Холодная ковка напрягает и деформирует металлы при температуре окружающей среды. С другой стороны, горячая ковка нагревает металлы вблизи или при температуре их плавления.
Перекристаллизация является ключом к температурному диапазону. Холодная ковка происходит до рекристаллизации, а горячая - после рекристаллизации.
Решение о выборе между холодной и горячей ковкой принимается на основе следующих факторов:
- Оборудование для производства и обработки: Чтобы получить максимальную отдачу от своего оборудования, производители специализируются на той или иной технике.
- Потребность клиентов: Инженеры принимают решение об оптимальной процедуре генерации идей на этапе проектирования при создании компонентов.
- Типы производимых компонентов: Конструкция детали\ часто определяет ограничения при выборе подходящей техники, так как определенные детали можно ковать только горячим способом. Другие же, напротив, идеально подходят для холодной ковки. Детали, изготовленные методом холодной ковки, имеют базовую конструкцию с небольшим количеством сложных деталей, в то время как детали, изготовленные методом горячей ковки, могут иметь невероятно точные микроскопические элементы.
Производители предпочитают холодную ковку везде, где это возможно, поскольку она требует меньше оборудования и не требует нагрева, что значительно снижает производственные затраты.
Резюме
Процесс ковки включает в себя нагрев, деформацию и отделку куска металла. Существует два вида ковки: холодная и горячая.
Холодная ковка может принимать различные формы, такие как холодная штамповка, гибка и холодное волочение, для производства широкого спектра изделий. С другой стороны, горячая ковка осуществляется путем нагрева металла выше температуры рекристаллизации для горячей штамповки.
Мы указали общие различия между процессами холодной и горячей ковки. Мы надеемся, что смогли упомянуть и конкретные различия между ними.